Polyethylene wood plastic and preparation method thereof
A technology of polyethylene and polyethylene wax, which is applied in the field of polyethylene wood-plastic and its preparation, can solve the problems of easy deformation and bending at high temperature, stress cracking, etc., achieve high temperature resistance to deformation, increase extrusion speed, and improve production efficiency Effect
- Summary
- Abstract
- Description
- Claims
- Application Information
AI Technical Summary
Problems solved by technology
Method used
Examples
Embodiment 1
[0026] A polyethylene wood plastic, the raw materials used are prepared according to the following parts by weight:
[0027] 35 parts of polyethylene, 60 parts of wood flour, 1.5 parts of maleic anhydride grafted polyethylene, 0.8 parts of polyethylene wax, 2 parts of zinc stearate, 2 parts of toner, 0.8 parts of antioxidant, anti-ultraviolet absorber UV-531 0.6 parts, 0.8 parts of stearic acid.
[0028] The antioxidant is antioxidant 168, namely tris[2,4-di-tert-butylphenyl]phosphite.
[0029] The anti-ultraviolet absorber UV-531 is 2-hydroxyl-4-n-octyloxybenzophenone.
[0030] A preparation method of polyethylene wood-plastic is carried out according to the following steps:
[0031] First send the wood flour and polyethylene into a high-speed mixer for heating and mixing, and then add the maleic anhydride grafted polyethylene, polyethylene wax, zinc stearate, toner, After antioxidant, anti-ultraviolet absorber UV-531 and stearic acid were mixed for 5 minutes, they were se...
Embodiment 2
[0036] A polyethylene wood plastic, the raw materials used are prepared according to the following parts by weight:
[0037] 30 parts of polyethylene, 50 parts of wood flour, 0.5 parts of maleic anhydride grafted polyethylene, 1 part of polyethylene wax, 1 part of zinc stearate, 3 parts of toner, 0.5 parts of antioxidant, anti-ultraviolet absorber UV-531 0.5 parts, 1 part of stearic acid.
[0038] The antioxidant is antioxidant 168, namely tris[2,4-di-tert-butylphenyl]phosphite.
[0039] The anti-ultraviolet absorber UV-531 is 2-hydroxyl-4-n-octyloxybenzophenone.
[0040] A preparation method of polyethylene wood-plastic is carried out according to the following steps:
[0041] First send the wood flour and polyethylene into a high-speed mixer for heating and mixing, and then add the maleic anhydride grafted polyethylene, polyethylene wax, zinc stearate, toner, After antioxidant, anti-ultraviolet absorber UV-531 and stearic acid were mixed for 5 minutes, they were sent to a...
Embodiment 3
[0046] A polyethylene wood plastic, the raw materials used are prepared according to the following parts by weight:
[0047] 40 parts of polyethylene, 70 parts of wood flour, 2 parts of maleic anhydride grafted polyethylene, 1.5 parts of polyethylene wax, 3 parts of zinc stearate, 6 parts of toner, 1 part of antioxidant, anti-ultraviolet absorber UV-531 0.9 parts, 1.2 parts of stearic acid.
[0048] The antioxidant is antioxidant B215.
[0049] The antioxidant B215 is a synergistic mixture of antioxidant 168 and antioxidant 1010.
[0050] The anti-ultraviolet absorber UV-531 is 2-hydroxyl-4-n-octyloxybenzophenone.
[0051] A preparation method of polyethylene wood-plastic is carried out according to the following steps:
[0052] First send the wood flour and polyethylene into a high-speed mixer for heating and mixing, and then add the maleic anhydride grafted polyethylene, polyethylene wax, zinc stearate, toner, After antioxidant, anti-ultraviolet absorber UV-531 and stearic...
PUM
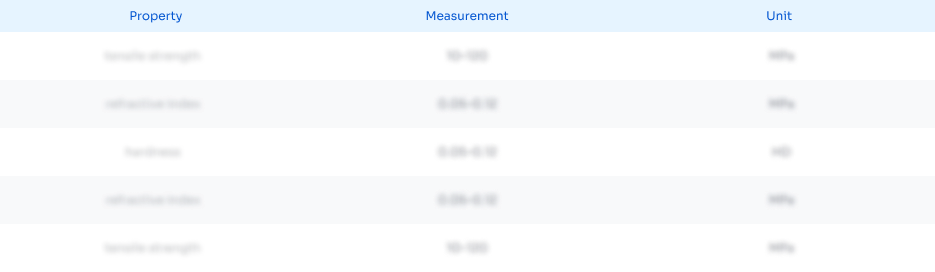
Abstract
Description
Claims
Application Information

- R&D
- Intellectual Property
- Life Sciences
- Materials
- Tech Scout
- Unparalleled Data Quality
- Higher Quality Content
- 60% Fewer Hallucinations
Browse by: Latest US Patents, China's latest patents, Technical Efficacy Thesaurus, Application Domain, Technology Topic, Popular Technical Reports.
© 2025 PatSnap. All rights reserved.Legal|Privacy policy|Modern Slavery Act Transparency Statement|Sitemap|About US| Contact US: help@patsnap.com