Nondestructive testing method for metal material fracture toughness
A metal material and fracture toughness technology, applied in the field of non-destructive testing of metal material fracture toughness, can solve the problems of time-consuming and laborious analysis process, unfavorable rapid detection and analysis, unable to reflect the mechanical properties of components, etc., achieving fast detection speed and low detection cost. , the effect of high detection accuracy
- Summary
- Abstract
- Description
- Claims
- Application Information
AI Technical Summary
Problems solved by technology
Method used
Image
Examples
Embodiment Construction
[0028] The technical concept of the present invention is as follows: the performance degradation of metal materials after thermal damage and fatigue creep damage is closely related to the nonlinear effect of ultrasonic propagation in materials, that is, material performance degradation is always accompanied by some form of material non-linearity. Linear mechanical behavior, which causes the generation of nonlinear harmonics in ultrasonic propagation. Dislocation String Model in metal materials (Dislocation String Model) [HikataA,Chick B,Elbaum C.Dislocation contribution to the second harmonic generation of ultrasonic waves.J.Appl.Phys.1965,36(1):229-236] It is believed that the dislocation-to-dislocation interaction in the crystal or the internal point defects will form pinning points on the dislocation line. On these pinning points, the dislocation line is not easy to move, but in the phase Between two adjacent pinning points, the dislocation line will produce forced vibratio...
PUM
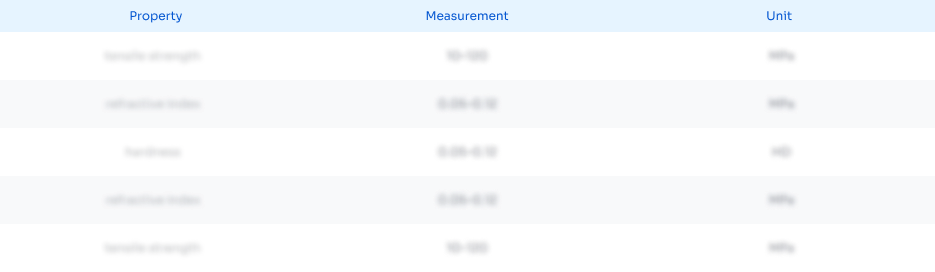
Abstract
Description
Claims
Application Information

- R&D
- Intellectual Property
- Life Sciences
- Materials
- Tech Scout
- Unparalleled Data Quality
- Higher Quality Content
- 60% Fewer Hallucinations
Browse by: Latest US Patents, China's latest patents, Technical Efficacy Thesaurus, Application Domain, Technology Topic, Popular Technical Reports.
© 2025 PatSnap. All rights reserved.Legal|Privacy policy|Modern Slavery Act Transparency Statement|Sitemap|About US| Contact US: help@patsnap.com