Method for restoring, roasting, purifying, and extracting manganese and iron by utilizing electrolytic manganese slag rotary kiln
A technology of electrolytic manganese waste slag and rotary kiln, applied in the direction of improving process efficiency, etc., can solve the problems of low element composition, difficult conversion, high separation cost, etc.
- Summary
- Abstract
- Description
- Claims
- Application Information
AI Technical Summary
Problems solved by technology
Method used
Image
Examples
Embodiment 1
[0019] The electrolytic manganese waste residue weight percentage 75% in Table 1 and the manganese ore tailings pond waste residue 25% in Table 2 are mixed to obtain manganese waste residue, after the coal gangue waste residue of Table 3 is added manganese waste residue by 5% of manganese waste residue gross weight and mixed, Join the rotary kiln, and carry out high-temperature roasting under the condition of high temperature environment and negative pressure of -0.012mp in the rotary kiln. The time is 1 hour, so that sulfur, ammonia and nitrogen compounds undergo physical and chemical changes, decompose into gaseous state, and are removed as the flue gas enters the multi-pipe dust removal, bag dust removal system and tail gas treatment system, and the tail gas containing sulfur, ammonia and nitrogen passes through Ammonification treatment (current technology), and then evaporated, crystallized, dehydrated and dried to make ammonium sulfate agricultural fertilizer, the waste he...
Embodiment 2
[0029] The electrolytic manganese waste residue weight percentage 65% in Table 1 and the manganese ore tailings pond waste residue 35% in Table 2 are mixed to obtain manganese waste residue, after the coal gangue waste residue of Table 3 is added manganese waste residue by 8% of manganese waste residue gross weight and mixed, Join the rotary kiln, and carry out high-temperature roasting under the condition of high temperature environment and negative pressure of -0.019 in the rotary kiln. The temperature inside the kiln is controlled at 950°C, the temperature at the kiln tail is 450°C, and the speed of the rotary kiln is controlled at 2 revolutions per minute. The roasting time Be 1.51 hours, following process is identical with embodiment 1.
[0030] The manganese powder composition (%) that embodiment 2 mentions
[0031] mn CaO MgO al 2 o 3 SiO 2 S 2 o 3 NH 3 -N 23.41 8.98 4.32 3.55 10.11 0.30 0.36-0.57
[0032] Embodiment 2 gained...
PUM
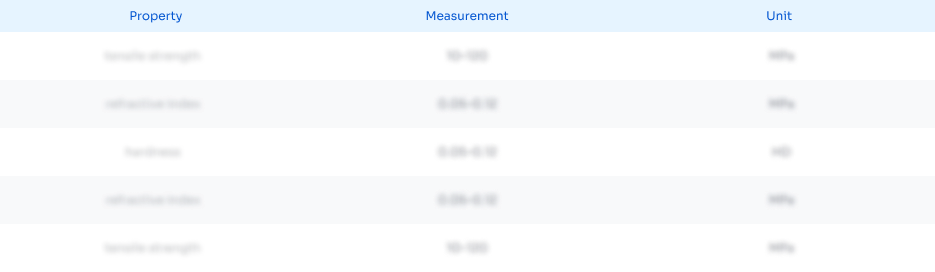
Abstract
Description
Claims
Application Information

- R&D Engineer
- R&D Manager
- IP Professional
- Industry Leading Data Capabilities
- Powerful AI technology
- Patent DNA Extraction
Browse by: Latest US Patents, China's latest patents, Technical Efficacy Thesaurus, Application Domain, Technology Topic, Popular Technical Reports.
© 2024 PatSnap. All rights reserved.Legal|Privacy policy|Modern Slavery Act Transparency Statement|Sitemap|About US| Contact US: help@patsnap.com