Preparation method of thermoplastic polyurethane elastomer
A thermoplastic polyurethane and elastomer technology, which is applied in the field of polymer preparation, can solve the problems of easy softening, decomposition, limited application scope, and decreased mechanical properties, etc., to increase heat resistance and anti-aging properties, increase heat resistance, The effect of improving mechanical properties
- Summary
- Abstract
- Description
- Claims
- Application Information
AI Technical Summary
Benefits of technology
Problems solved by technology
Method used
Examples
Embodiment 1
[0027] A kind of preparation method of thermoplastic polyurethane elastomer provided by the present embodiment, comprises the following steps:
[0028] In the first step, 30wt% of 1,4-cyclohexane diisocyanate, 60wt% of polyethylene adipate (molecular weight of 3000), 8wt% of chain extender 1,4-butanediol, 0.5 wt% lubricant stearamide wax, 0.5wt% antioxidant β-(4-hydroxy-3,5-di-tert-butylphenyl) n-octadecyl propionate, 0.05wt% titanium system catalyst, 0.5wt% of bis(2,2,6,6-tetramethyl-4-piperidinyl) sebacate and 0.45wt% of carbodiimide hydrolysis resistance agent in the mixer After fully stirring at 100°C for 20 minutes, fully masticate at 140°C in a high-temperature plastic machine or internal mixer, and obtain a thermoplastic polyurethane elastomer matrix after drying.
[0029] In the second step, the nano-SiO 2 Filler, γ-methacryloxypropyltrimethoxysilane, cyclohexane and n-propylamine are added to the reaction vessel according to the mass ratio of 1:15:10:10, stirred at ...
Embodiment 2
[0032] A kind of preparation method of thermoplastic polyurethane elastomer provided by the present embodiment, comprises the following steps:
[0033] The first step, the 1,4-cyclohexane diisocyanate of 40wt%, the polyethylene adipate of 50wt%, the chain extender 1,4-butanediol of 6wt%, the lubricant of 2wt% Denier wax, 0.3wt% antioxidant tetrakis[β-(3,5-di-tert-butyl-4-hydroxyphenyl) propionate] pentaerythritol ester, 0.005wt% bismuth catalyst, 1.2wt% bis( 2,2,6,6-Tetramethyl-4-piperidinyl) sebacate and 0.495wt% carbodiimide hydrolysis resistance agent were placed in a mixer at 110°C for 10 minutes and then fully stirred , in a high-temperature plastic machine or internal mixer, fully masticated at 155 ° C, and obtained a thermoplastic polyurethane elastomer matrix after drying.
[0034] In the second step, the nano-TiO 2Filler, γ-methacryloxypropyltrimethoxysilane, cyclohexane and n-propylamine were added to the reaction vessel according to the mass ratio of 1:20:15:15, s...
Embodiment 3
[0037] A kind of preparation method of thermoplastic polyurethane elastomer provided by the present embodiment, comprises the following steps:
[0038] In the first step, 20wt% of 1,4-cyclohexane diisocyanate, 70wt% of polyethylene adipate (molecular weight of 3000), 5wt% of chain extender 1,4-butanediol, 3wt% % lubricant montan wax, 0.2wt% antioxidant bis[(2,4-di-tert-butylphenyl) phosphite] pentaerythritol ester, 0.02wt% bismuth catalyst, 0.28wt% bis(2 , 2,6,6-tetramethyl-4-piperidinyl) sebacate and 1.5wt% carbodiimide hydrolysis-resistant agent were placed in a mixer at 90 ° C for 30 minutes, Fully masticate at 130°C in a high-temperature plastic machine or internal mixer, and obtain a thermoplastic polyurethane elastomer matrix after drying.
[0039] In the second step, add nano-MgO filler, γ-methacryloxypropyltrimethoxysilane, cyclohexane and n-propylamine into the reaction vessel according to the mass ratio of 1:10:3:3, and stir at room temperature for 10 minutes , the...
PUM
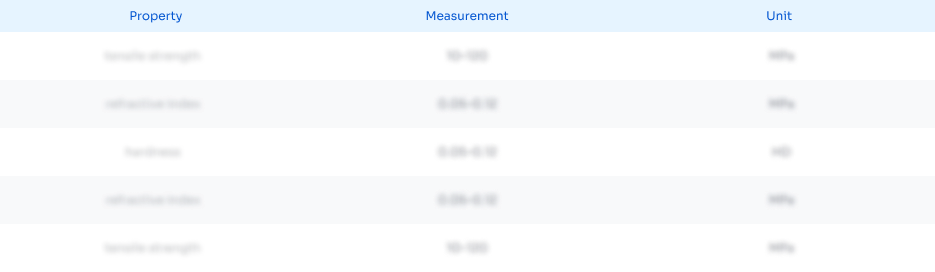
Abstract
Description
Claims
Application Information

- R&D
- Intellectual Property
- Life Sciences
- Materials
- Tech Scout
- Unparalleled Data Quality
- Higher Quality Content
- 60% Fewer Hallucinations
Browse by: Latest US Patents, China's latest patents, Technical Efficacy Thesaurus, Application Domain, Technology Topic, Popular Technical Reports.
© 2025 PatSnap. All rights reserved.Legal|Privacy policy|Modern Slavery Act Transparency Statement|Sitemap|About US| Contact US: help@patsnap.com