Lignite pre-drying process and lignite pre-drying device
A pre-drying and lignite technology, applied in the direction of drying gas arrangement, drying solid materials, non-progressive dryers, etc., can solve the problems that affect large-scale industrial utilization, spontaneous combustion dust, low output, etc., and achieve the benefit of large-scale industrial application , Reduce transportation costs, large heat exchange area
- Summary
- Abstract
- Description
- Claims
- Application Information
AI Technical Summary
Problems solved by technology
Method used
Image
Examples
Embodiment Construction
[0020] Below in conjunction with accompanying drawing, device of the present invention is further explained:
[0021] The lignite pre-drying device includes a crushed coal bunker 1, a coal feeder 2 and a tubular dryer 3 connected in sequence, the coal inlet of the tubular dryer 3 is connected to the coal feeder 2, and the tail gas outlet 2.3 is connected to the bag filter The tail gas inlet 4.1 of the connection 4 is connected, the tail gas outlet 4.2 of the bag filter 4 is connected with the induced draft fan 6, the dust outlet 4.3 and the coal outlet 3.2 of the tubular dryer 3 are connected with the qualified coal removal downstream device 5. The bag filter 4 is preferably a long bag low pressure large jet bag filter.
[0022] Process example
[0023] The crushed coal with a water content of 32-41Wt% and a particle size of 8 mm or less is cached in the bunker 1, fed into the drying tube of the tube dryer 3 through the coal feeder 2, and fed to the tube dryer 3 at the same t...
PUM
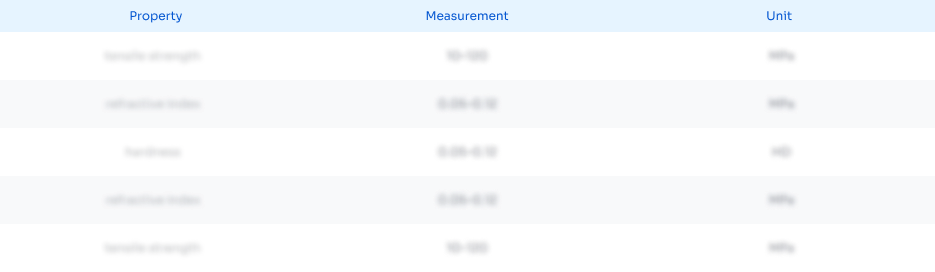
Abstract
Description
Claims
Application Information

- Generate Ideas
- Intellectual Property
- Life Sciences
- Materials
- Tech Scout
- Unparalleled Data Quality
- Higher Quality Content
- 60% Fewer Hallucinations
Browse by: Latest US Patents, China's latest patents, Technical Efficacy Thesaurus, Application Domain, Technology Topic, Popular Technical Reports.
© 2025 PatSnap. All rights reserved.Legal|Privacy policy|Modern Slavery Act Transparency Statement|Sitemap|About US| Contact US: help@patsnap.com