A New Process for Reducing Formaldehyde Consumption in Neopentyl Glycol Production
A neopentyl glycol and new process technology, which is applied in the new process field of reducing formaldehyde consumption in the production of neopentyl glycol, can solve the problems of poor quality hydrogenation method, low price, poor high temperature thermal stability, etc., and achieve the reduction of side effects Response, consumption reduction effect
- Summary
- Abstract
- Description
- Claims
- Application Information
AI Technical Summary
Problems solved by technology
Method used
Examples
Embodiment 1
[0028] A new process for reducing formaldehyde consumption in the production of neopentyl glycol. Add 2000-3000L of water to the 5000L enamel (or stainless steel) condensation reaction kettle, feed cooling water into the reactor jacket and cooling coil, start stirring and add 37% Formaldehyde 24Kmol, then add 97-98% isobutyraldehyde 8Kmol, open the alkali addition valve at 15-25°C at room temperature, add half of the total amount of 30% NaOH solution 4.12Kmol, the speed of alkali addition should be adjusted according to the temperature of the kettle, When adding alkali, the temperature in the kettle is controlled at 30-35°C, pH9-11, and the time is 2 hours. The temperature in the condensation reactor rises rapidly, exceeding the allowable temperature range, which is not conducive to the condensation reaction, and easily causes the disproportionation reaction of formaldehyde, which increases the consumption of formaldehyde; Alcohol, the hydroxyl value of the image product); the...
Embodiment 2
[0031]A new process for reducing formaldehyde consumption in the production of neopentyl glycol. In a 5000L enamel (or stainless steel) condensation reaction kettle, 2% to 5% is put in to recover 2000 to 3000L of dilute formaldehyde, and the dilute formaldehyde feed is turned off after adding dilute formaldehyde. valve, measure the content of dilute formaldehyde in the condensation kettle, calculate the feeding amount of 37% formaldehyde according to the content of dilute formaldehyde and the feeding amount, pass cooling water to the jacket of the condensation reaction kettle and the cooling coil, start stirring and add 37% formaldehyde Make the total amount of formaldehyde including the formaldehyde in the dilute formaldehyde in the condensation reaction kettle to be 28Kmol, then add 8Kmol of 97-98% isobutyraldehyde, open the alkali adding valve at normal temperature of 15~25 ℃, add 30% of the total amount of NaOH solution. Half of 4.2Kmol, the speed of adding alkali should be...
Embodiment 3
[0034] A new process for reducing formaldehyde consumption in the production of neopentyl glycol. In a 5000L enamel (or stainless steel) condensation reaction kettle, 2000-3000L of dilute formaldehyde recovered by 2% to 5% is put into it, and the dilute formaldehyde is turned off after adding the dilute formaldehyde. Feed valve, measure the content of dilute formaldehyde in the condensation kettle, calculate the feeding amount of 37% formaldehyde according to the content and feeding amount of dilute formaldehyde, pass cooling water to the jacket of the reactor and the cooling coil, start stirring and add 37% formaldehyde Make the total amount of formaldehyde including the formaldehyde in the dilute formaldehyde in the condensation reaction kettle to be 20Kmol, then add 8Kmol of 97-98% isobutyraldehyde, open the alkali adding valve at normal temperature of 15~25 ℃, add 30% of the total amount of NaOH solution. Half of 4.04Kmol, the speed of adding alkali should be adjusted accor...
PUM
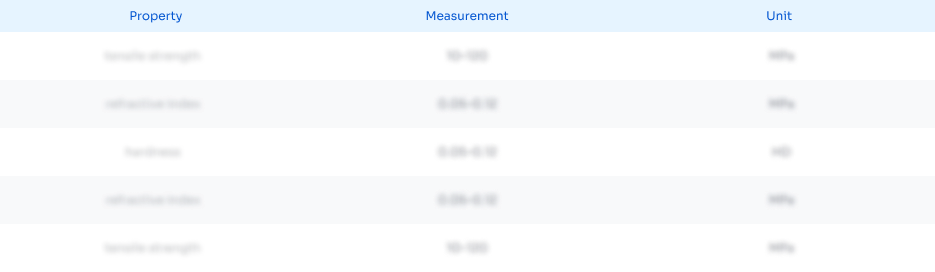
Abstract
Description
Claims
Application Information

- R&D
- Intellectual Property
- Life Sciences
- Materials
- Tech Scout
- Unparalleled Data Quality
- Higher Quality Content
- 60% Fewer Hallucinations
Browse by: Latest US Patents, China's latest patents, Technical Efficacy Thesaurus, Application Domain, Technology Topic, Popular Technical Reports.
© 2025 PatSnap. All rights reserved.Legal|Privacy policy|Modern Slavery Act Transparency Statement|Sitemap|About US| Contact US: help@patsnap.com