Control method and device of electric precipitator in sintering system
A technology of electrostatic precipitator and rapping device, applied in the direction of power supply technology, electrostatic separation, etc., can solve problems such as energy waste, achieve the effects of avoiding waste of electric energy, overcoming waste of electric energy, and reducing energy consumption of dust removal
- Summary
- Abstract
- Description
- Claims
- Application Information
AI Technical Summary
Problems solved by technology
Method used
Image
Examples
Embodiment 1
[0066] Due to changes in production, the flow rate and dust content of the exhaust gas in the main flue of the sintering machine will also change greatly. The general electrostatic precipitator is designed to consider the dust removal requirements under the maximum production capacity, so many times the actual The working condition has not reached full load, and the electrostatic precipitator is still working at full load at this time, resulting in a lot of waste of electric energy. Even if the electrostatic precipitator is adjusted according to experience, it is obvious that the effect of energy saving will basically not be achieved due to large errors. However, in this embodiment, through the acquisition and analysis of field working condition data, more accurate control of the electrostatic precipitator is realized, and energy consumption for dust removal is reduced.
[0067] The electrostatic precipitator is a metal anode and cathode with a large difference in curvature ra...
Embodiment 2
[0106] The operation process of electrostatic precipitator is a dynamic process, and different working conditions should have different optimal operating parameters and different operating modes. As the amount of material increases, the high specific resistance dust in the flue gas dust also increases. Back corona is prone to occur during the dust collection process, resulting in a sharp drop in dust removal efficiency.
[0107] Theory and practice show that intermittent pulse power supply can effectively overcome the back corona caused by dust with high specific resistance, and the duty ratio of intermittent pulse power supply is 1:2, 1:4, 1:6, 1:8...1:20 and 2:2, 2:4, 2:6, 2:8...2:20 etc. In this embodiment, a duty ratio setting database can be established according to the on-site production conditions and the volt-ampere characteristics of the electric field. Then after the amount of sintering material is obtained, compare the data of the amount of sintering material with t...
Embodiment 3
[0112] Too much or too little rapping will greatly affect the dust removal effect. If the frequency of rapping is too small, it will cause serious dust accumulation on the dust collection plate, resulting in a serious decrease in the secondary current and a decrease in the dust removal efficiency. Too much rapping will cause secondary dust in the electric field, resulting in a decrease in dust removal efficiency. Therefore, proper rapping control can not only ensure the operation of the dust collector in a high-efficiency state, but also achieve energy-saving effects.
[0113] see Figure 5 As shown, on the basis of Embodiment 1, the electrostatic precipitator may also include a rapping device, and after step S301, the method may also include the following steps:
[0114] S309. Obtain a third correlation coefficient between the amount of sintered material and the rapping frequency.
[0115] S310. Obtain a rapping frequency by multiplying the amount of sintered material by t...
PUM
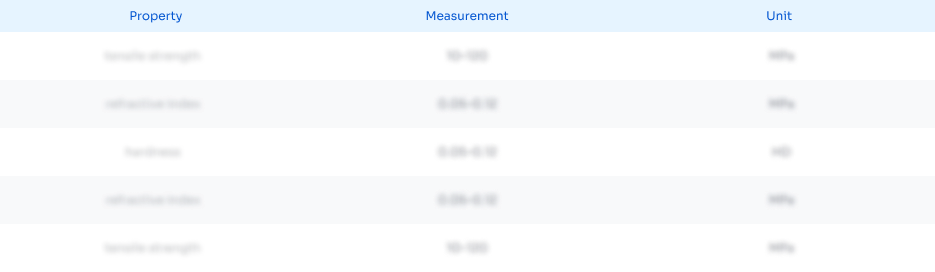
Abstract
Description
Claims
Application Information

- R&D
- Intellectual Property
- Life Sciences
- Materials
- Tech Scout
- Unparalleled Data Quality
- Higher Quality Content
- 60% Fewer Hallucinations
Browse by: Latest US Patents, China's latest patents, Technical Efficacy Thesaurus, Application Domain, Technology Topic, Popular Technical Reports.
© 2025 PatSnap. All rights reserved.Legal|Privacy policy|Modern Slavery Act Transparency Statement|Sitemap|About US| Contact US: help@patsnap.com