Technology for operating bulk stacking baking fragrance on tobacco baking controller through ten steps
A controller and roaster technology, applied in application, tobacco, preparation of tobacco, etc., can solve the problems of poor quality, large difference in process curve, stiff and smooth tobacco leaves, etc.
- Summary
- Abstract
- Description
- Claims
- Application Information
AI Technical Summary
Problems solved by technology
Method used
Image
Examples
Embodiment Construction
[0092] The following is a further description of the present invention's ten-step operation on the tobacco leaf curing controller to stack and burn incense with scattered leaves.
[0093] The present invention adopts a ten-step process of stacking and stacking fragrant leaves on the tobacco leaf curing controller, sets numbers for the roasting aroma of the lower, middle and upper tobacco leaves on the tobacco leaf curing controller respectively, and combines them into a roasting aroma process curve. For the roasted aromas of dry-day tobacco leaves, rainy-water tobacco leaves, dry-yellow tobacco leaves, and high-altitude late-maturing tobacco leaves formed under special climatic conditions, numbers are set on the tobacco leaf roaster and combined into a roasting aroma process curve. After checking the aroma of tobacco leaves during the changing process of tobacco leaf curing, fine-tune the setting numbers on the tobacco leaf roaster respectively, and combine them into a roastin...
PUM
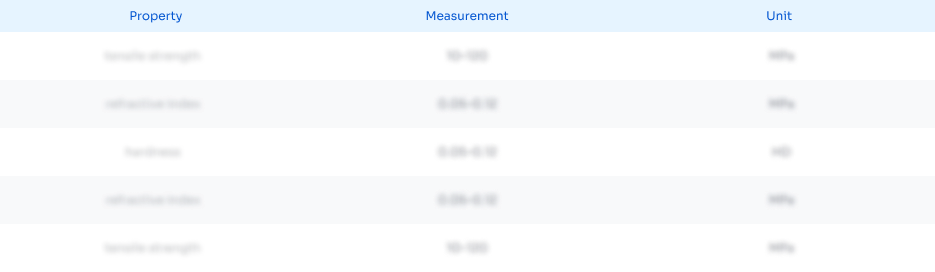
Abstract
Description
Claims
Application Information

- R&D
- Intellectual Property
- Life Sciences
- Materials
- Tech Scout
- Unparalleled Data Quality
- Higher Quality Content
- 60% Fewer Hallucinations
Browse by: Latest US Patents, China's latest patents, Technical Efficacy Thesaurus, Application Domain, Technology Topic, Popular Technical Reports.
© 2025 PatSnap. All rights reserved.Legal|Privacy policy|Modern Slavery Act Transparency Statement|Sitemap|About US| Contact US: help@patsnap.com