Heat pipe radiator of phase change drive loop
A loop heat pipe and radiator technology, applied in indirect heat exchangers, lighting and heating equipment, etc., can solve the problems of vapor-liquid interface deviation, large operating flow resistance, and increased flow resistance, and achieve the elimination of contact thermal resistance , Strengthen the effect of liquid film convection heat transfer
- Summary
- Abstract
- Description
- Claims
- Application Information
AI Technical Summary
Problems solved by technology
Method used
Image
Examples
Embodiment Construction
[0009] The principle and structure of the present invention will be further described below in conjunction with the accompanying drawings and through specific embodiments. It should be noted that this embodiment is descriptive rather than restrictive, and the protection scope of the present invention is not limited by this embodiment.
[0010] Phase change drive loop heat pipe radiator, its structure is that the upper part of the evaporation section of the heat pipe is provided with a liquid-absorbing core, the bottom of the evaporation section is a heating surface, the inlet of the working medium circulation pipe is connected to the liquid-absorbing core; the outlet of the working medium circulation pipe is connected to the In the space interlayer formed by the liquid-absorbing core and the heating surface. A liquid storage tank is arranged between the inlet of the working fluid circulation pipe and the liquid-absorbing core. The evaporating section of the heat pipe is a fla...
PUM
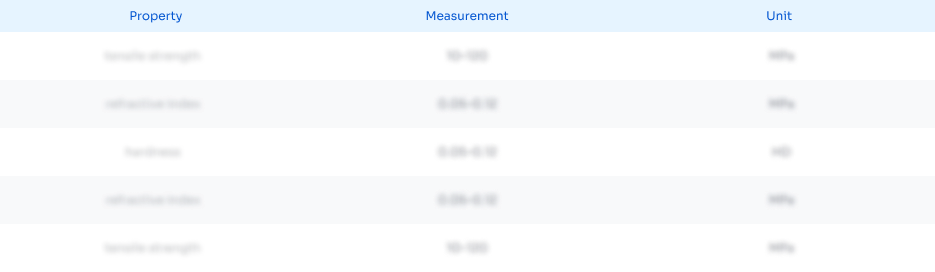
Abstract
Description
Claims
Application Information

- R&D Engineer
- R&D Manager
- IP Professional
- Industry Leading Data Capabilities
- Powerful AI technology
- Patent DNA Extraction
Browse by: Latest US Patents, China's latest patents, Technical Efficacy Thesaurus, Application Domain, Technology Topic, Popular Technical Reports.
© 2024 PatSnap. All rights reserved.Legal|Privacy policy|Modern Slavery Act Transparency Statement|Sitemap|About US| Contact US: help@patsnap.com