Continuous tubular plug flow reactor and preparation method for preparing continuous bulk SAN (Styrene-Acrylonitrile) resin
A plug-flow reactor and reactor technology, which is applied in the field of polymer material synthesis and preparation, can solve problems such as product performance fluctuations, production processes, and operating conditions and equipment parameters, and achieve excellent processing performance, narrow molecular weight distribution, and impact high intensity effect
- Summary
- Abstract
- Description
- Claims
- Application Information
AI Technical Summary
Problems solved by technology
Method used
Image
Examples
Embodiment 1
[0020] The prepared raw material solution, initiator and chain transfer agent are transported to the inlet of the first plug flow reactor of each group of two-stage continuous tubular plug flow reactors according to a certain ratio, and at the same time, each group of two-stage continuous tubular plug flow reactors The recycle material split at the outlet of the second plug flow reactor of the flow reactor also enters the first plug flow reactor together. The temperatures of the upper, middle and lower zones of the first plug flow reactor were 124.5°C, 127.8°C, and 130.5°C, respectively. The temperatures in the upper, middle and lower zones of the second plug flow reactor are 135.9°C, 141.2°C, and 148.8°C, respectively. The weight ratio of styrene and acrylonitrile in the raw material liquid is 76:24, and its flow rate is controlled to be 100g / h. The concentration of the initiator solution is 70ppm, and the flow rate is controlled at 0.7g / h. The concentration of the chain tr...
Embodiment 2
[0028]The prepared raw material solution, initiator and chain transfer agent are transported to the inlet of the first plug flow reactor of each group of two-stage continuous tubular plug flow reactors according to a certain ratio, and at the same time, each group of two-stage continuous tubular plug flow reactors The recycle material split at the outlet of the second plug flow reactor of the flow reactor also enters the first plug flow reactor together. The temperatures of the upper, middle and lower zones of the first plug flow reactor were 125.2°C, 128.1°C, and 131.6°C, respectively. The temperatures in the upper, middle and lower zones of the second plug flow reactor were 135.9°C, 141.8°C, and 147.8°C, respectively. The weight ratio of styrene and acrylonitrile in the raw material liquid is 76:24, and its flow rate is controlled to be 100g / h. The concentration of the initiator solution is 70ppm, and the flow rate is controlled at 0.7g / h. The concentration of the chain tr...
Embodiment 3
[0035] The prepared raw material solution, initiator and chain transfer agent are transported to the inlet of the first plug flow reactor of each group of two-stage continuous tubular plug flow reactors according to a certain ratio, and at the same time, each group of two-stage continuous tubular plug flow reactors The recycle material split at the outlet of the second plug flow reactor of the flow reactor also enters the first plug flow reactor together. The temperatures of the upper, middle and lower zones of the first plug flow reactor were 125.5°C, 127.9°C, and 131.6°C, respectively. The temperatures in the upper, middle and lower zones of the second plug flow reactor are 135.7°C, 140.9°C, and 149.1°C, respectively. The weight ratio of styrene and acrylonitrile in the raw material liquid is 76:24, and its flow rate is controlled to be 100g / h. The concentration of the initiator solution is 70ppm, and the flow rate is controlled at 0.7g / h. The concentration of the chain tr...
PUM
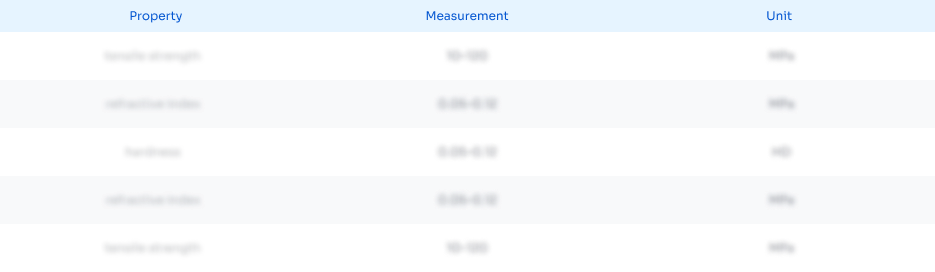
Abstract
Description
Claims
Application Information

- R&D
- Intellectual Property
- Life Sciences
- Materials
- Tech Scout
- Unparalleled Data Quality
- Higher Quality Content
- 60% Fewer Hallucinations
Browse by: Latest US Patents, China's latest patents, Technical Efficacy Thesaurus, Application Domain, Technology Topic, Popular Technical Reports.
© 2025 PatSnap. All rights reserved.Legal|Privacy policy|Modern Slavery Act Transparency Statement|Sitemap|About US| Contact US: help@patsnap.com