A kind of regeneration method of deactivated SCR denitrification catalyst
A denitrification catalyst and catalyst technology, applied in the direction of catalyst regeneration/reactivation, chemical instruments and methods, physical/chemical process catalysts, etc., can solve the problems of poor catalyst activity and anti-toxic performance, easy deactivation again, and complicated treatment. Achieve good stability, promote activity and prolong service life
- Summary
- Abstract
- Description
- Claims
- Application Information
AI Technical Summary
Problems solved by technology
Method used
Examples
Embodiment 1
[0025] (1) Preparation of regeneration solution: prepare the regeneration solution containing 0.1mol / L of sulfuric acid, 0.1mol / L of ferric nitrate and 0.1mol / L of cerium nitrate, and add a small amount of oxalic acid, citric acid and diffusing agent. Vibrate ultrasonically for 20 minutes to form a homogeneous mixture.
[0026] (2) Preparation of anti-toxic modification liquid: prepare zinc nitrate 0.1mol / L, antimony acetate 0.5mol / L, niobium oxalate 0.5mol / L, add a small amount of methanol and diffusing agent, and use ultrasonic vibration for 20min to make it Mix well.
[0027] (3) Take a deactivated catalyst from a coal-fired power plant and cut it into a piece of 2.1×2.1×20 (cm), and blow it with oil-free compressed air (0.6MPa) for 30 minutes.
[0028] (4) Immerse the above-mentioned catalyst in the regeneration solution for 3 hours, vibrate with ultrasonic waves, and then put it into a drying oven for 2 hours at 110°C.
[0029] (5) Immerse the above-mentioned dry cataly...
Embodiment 2
[0032] (1) Preparation of regeneration solution: prepare regeneration solution containing 0.1mol / L of sulfuric acid, 0.5mol / L of ferric nitrate and 0.5mol / L of cerium nitrate, and add a small amount of oxalic acid, citric acid and diffusing agent. Vibrate ultrasonically for 20 minutes to form a homogeneous mixture.
[0033] (2) Preparation of anti-toxic modification liquid: prepare zinc nitrate 0.1mol / L, antimony acetate 0.5mol / L, niobium oxalate 0.5mol / L, add a small amount of methanol and diffusing agent, and use ultrasonic vibration for 20min to make it Mix well.
[0034] (3) Take a deactivated catalyst from a coal-fired power plant and cut it into a piece of 2.1×2.1×20 (cm), and blow it with oil-free compressed air (0.6MPa) for 30 minutes.
[0035] (4) Immerse the above-mentioned catalyst in the regeneration solution for 3 hours, vibrate with ultrasonic waves, and then put it into a drying oven for 2 hours at 110°C.
[0036] (5) Immerse the above-mentioned dry catalyst i...
Embodiment 3
[0039] (1) Preparation of regeneration solution: Prepare regeneration solution containing 0.1mol / L of sulfuric acid, 1mol / L of ferric nitrate and 1 mol / L of cerium nitrate, and add a small amount of oxalic acid, citric acid and diffusing agent. Vibrate ultrasonically for 20 minutes to form a homogeneous mixture.
[0040] (2) Preparation of anti-toxic modification liquid: prepare zinc nitrate 0.1mol / L, antimony acetate 0.5mol / L, niobium oxalate 0.5mol / L, add a small amount of methanol and diffusing agent, and use ultrasonic vibration for 20min to make it Mix well.
[0041] (3) Take a deactivated catalyst from a coal-fired power plant and cut it into a piece of 2.1×2.1×20 (cm), and blow it with oil-free compressed air (0.6MPa) for 30 minutes.
[0042] (4) Immerse the above catalyst in the regenerated solution for 3 hours, vibrate with ultrasonic waves, and then put it into a drying oven for 2 hours at 110°C.
[0043] (5) Immerse the above-mentioned dried catalyst in the anti-t...
PUM
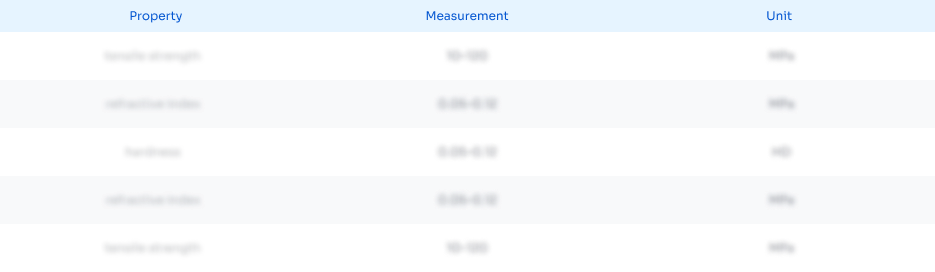
Abstract
Description
Claims
Application Information

- R&D
- Intellectual Property
- Life Sciences
- Materials
- Tech Scout
- Unparalleled Data Quality
- Higher Quality Content
- 60% Fewer Hallucinations
Browse by: Latest US Patents, China's latest patents, Technical Efficacy Thesaurus, Application Domain, Technology Topic, Popular Technical Reports.
© 2025 PatSnap. All rights reserved.Legal|Privacy policy|Modern Slavery Act Transparency Statement|Sitemap|About US| Contact US: help@patsnap.com