Soaking-centrifugalizing equipment
A technology of centrifugal equipment and centrifugal device, which is applied in the direction of coating and liquid coating on the surface, etc., which can solve the problems of poor process repeatability, limited filter tube length, poor product performance, etc., and achieve recycling and reuse , Easy to use, easy to install and arrange
- Summary
- Abstract
- Description
- Claims
- Application Information
AI Technical Summary
Problems solved by technology
Method used
Image
Examples
Embodiment Construction
[0031] Such as figure 1 As shown, the present invention includes a base 1, an immersion centrifuge device and a slurry recovery device 7 located on one side of the base 1 and capable of moving back and forth in the horizontal direction. The impregnation centrifugal device includes a clamping tool 5 capable of continuous rotation and driving the foam filter tube precursor 8 to rotate synchronously while continuously rotating, and an impregnation device 2 installed on the base 1 and capable of moving up and down in the vertical direction , Drive the rotary drive motor 3-1 for continuous rotation of the clamping tooling 5 and the control system 6 for controlling and adjusting the steering and speed of the rotary drive motor 3-1, the rotary drive motor 3-1 is installed on the base 1, The clamping tool 5 is arranged above the base 1 . The power output shaft of the rotary drive motor 3-1 is connected to the clamping tool 5 through a transmission mechanism, the clamping tool 5 is ar...
PUM
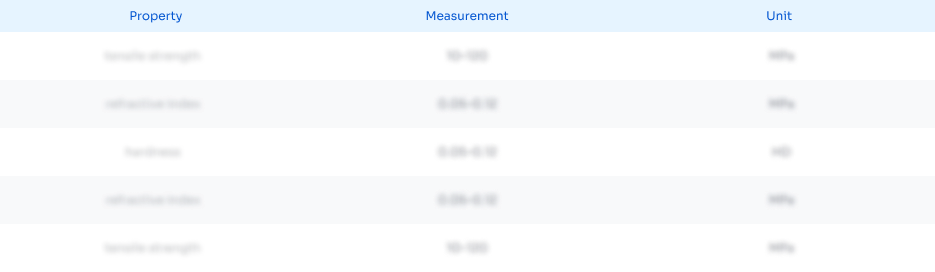
Abstract
Description
Claims
Application Information

- R&D
- Intellectual Property
- Life Sciences
- Materials
- Tech Scout
- Unparalleled Data Quality
- Higher Quality Content
- 60% Fewer Hallucinations
Browse by: Latest US Patents, China's latest patents, Technical Efficacy Thesaurus, Application Domain, Technology Topic, Popular Technical Reports.
© 2025 PatSnap. All rights reserved.Legal|Privacy policy|Modern Slavery Act Transparency Statement|Sitemap|About US| Contact US: help@patsnap.com