Hydrodynamic retarder
A hydraulic retarder and transmission spindle technology, applied in the direction of liquid resistance brakes, brake types, mechanical equipment, etc., can solve the problems of high manufacturing cost, shortened service life of gear pump gears, shortened service life of hydraulic oil, etc., to improve sensitivity Sex and response speed, reasonable structure design, and the effect of prolonging the service life
- Summary
- Abstract
- Description
- Claims
- Application Information
AI Technical Summary
Problems solved by technology
Method used
Image
Examples
Embodiment 1
[0068] Embodiment 1: as figure 1 , 2 , 3, 4, 5, and 6, a hydraulic retarder includes a housing 1 and a transmission main shaft 2, and a front rotating impeller 3 and a rear rotating impeller 4 are arranged on the transmission main shaft 2, and on the housing 1 A brake pressure regulating switch, a gear pump and a water pump are provided, the gear pump is connected to the transmission main shaft, the water pump is connected to the gear pump, the front rotating impeller 3 is connected to the transmission main shaft 2 through the moving wheel flange 5, and the rear rotating impeller 4 It is connected with the transmission main shaft 2 through the planetary gear set, and the front rotating impeller 3 is uniformly provided with oil inlet holes 6 and oil outlet holes 7 .
[0069] Wherein, the above-mentioned front rotating impeller 3 includes a body A8, and arc-shaped blades A9 are uniformly arranged on the inner surface of the body A8, and the oil inlet hole 6 is arranged at the m...
PUM
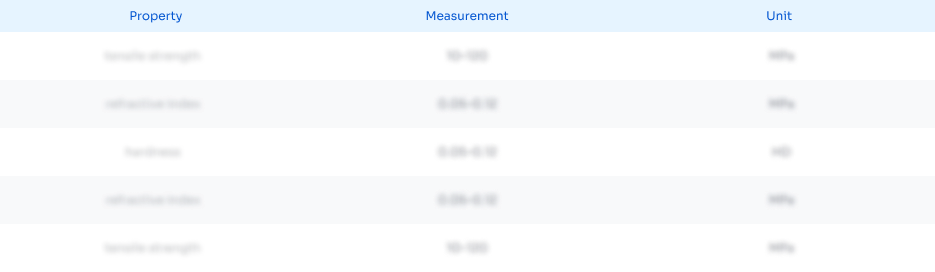
Abstract
Description
Claims
Application Information

- Generate Ideas
- Intellectual Property
- Life Sciences
- Materials
- Tech Scout
- Unparalleled Data Quality
- Higher Quality Content
- 60% Fewer Hallucinations
Browse by: Latest US Patents, China's latest patents, Technical Efficacy Thesaurus, Application Domain, Technology Topic, Popular Technical Reports.
© 2025 PatSnap. All rights reserved.Legal|Privacy policy|Modern Slavery Act Transparency Statement|Sitemap|About US| Contact US: help@patsnap.com