Method for preparing 1,1-difluoroethylene by cracking of 1,1,1-difluoro-1-chloroethane
A technology of difluoro-chloroethane and difluoroethylene, applied in the direction of dehydrohalogenation preparation, etc., can solve the problems of limited improvement effect, easy deactivation, catalyst loss, etc., to improve gas flow and heat distribution, and eliminate local Overheating phenomenon, the effect of improving the reaction conversion rate
- Summary
- Abstract
- Description
- Claims
- Application Information
AI Technical Summary
Problems solved by technology
Method used
Image
Examples
Embodiment 1
[0048] Evenly fill the internal components in the Ф32×1200mm quartz cracking tube, and the filling volume is 500m3 of the external area of the internal components per cubic meter of reaction tube volume 2 (Internal component composition: nickel content 100%); put the cracking tube into the electric heating furnace, turn on the electric heating, and preheat the cracking tube to 500°C. Maintain the temperature of the cracking tube at 500°C, control the flow rate of the raw material 1,1,1-difluoromonochloroethane so that the residence time in the effective constant temperature heating section of the cracking tube (length 570mm) is 200s; mix the reacted The gas is rapidly cooled to below 100°C by a water cooler, and then the acid gas produced by cracking is washed away by the secondary water washing tower and the first alkali washing tower, and then the moisture is removed by freeze drying. After the gas is collected, the composition is detected by gas chromatography.
[0049] T...
Embodiment 2
[0052] Evenly fill the internal components in the Ф32×1200mm quartz cracking tube, and the filling amount is 100m3 of the external area of the internal components per cubic meter of reaction tube volume 2 (Internal component composition: nickel content 100%); put the cracking tube into the electric heating furnace, turn on the electric heating, and preheat the cracking tube to 580°C. Maintain the temperature of the cracking tube at 580°C, control the flow rate of the raw material 1,1,1-difluorochloroethane so that the residence time in the effective constant temperature heating section of the cracking tube (length 570mm) is 100s; mix the reacted The gas is rapidly cooled to below 100°C by a water cooler, and then the acid gas produced by cracking is washed away by the secondary water washing tower and the first alkali washing tower, and then the moisture is removed by freeze drying. After the gas is collected, the composition is detected by gas chromatography.
[0053] The m...
Embodiment 3
[0056] Evenly fill the internal components in the Ф32×1200mm quartz cracking tube, and the filling amount is 300m3 of the external area of the internal components per cubic meter of reaction tube volume 2 (Internal component composition: 90% nickel, 10% iron); put the cracking tube into the electric heating furnace, turn on the electric heating, and preheat the cracking tube to 560°C. Maintain the temperature of the cracking tube at 560°C, control the flow rate of the raw material 1,1,1-difluorochloroethane so that the residence time in the effective constant temperature heating section of the cracking tube (length 570mm) is 80s; mix the reacted The gas is rapidly cooled to below 100°C by a water cooler, and then the acid gas produced by cracking is washed away by the secondary water washing tower and the first alkali washing tower, and then the moisture is removed by freeze drying. After the gas is collected, the composition is detected by gas chromatography.
[0057] The m...
PUM
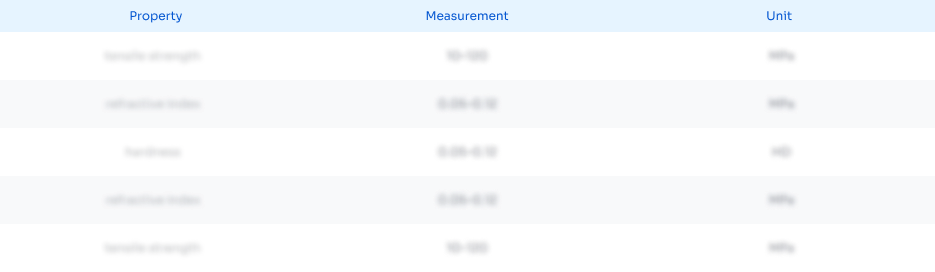
Abstract
Description
Claims
Application Information

- R&D
- Intellectual Property
- Life Sciences
- Materials
- Tech Scout
- Unparalleled Data Quality
- Higher Quality Content
- 60% Fewer Hallucinations
Browse by: Latest US Patents, China's latest patents, Technical Efficacy Thesaurus, Application Domain, Technology Topic, Popular Technical Reports.
© 2025 PatSnap. All rights reserved.Legal|Privacy policy|Modern Slavery Act Transparency Statement|Sitemap|About US| Contact US: help@patsnap.com