Garbage burning equipment with forward-pushing three-section type cooling high-pressure loss fire grate and method for burning garbage by using garbage burning equipment
A three-stage cooling and waste incineration technology, applied in combustion methods, lighting and heating equipment, incinerators, etc., can solve the problems of incinerator output, decreased operation efficiency, unattainable operation and maintenance costs, and unsatisfactory slag leakage rate. Achieve improved performance, ease of control, and long service life
- Summary
- Abstract
- Description
- Claims
- Application Information
AI Technical Summary
Problems solved by technology
Method used
Image
Examples
Embodiment Construction
[0013] Such as figure 1 -4 shows a garbage incineration equipment that adopts three-stage cooling and high-pressure loss grate in succession. A sliding grate 101, a fixed grate 102, and a blanking grate 103 are set in the grate type garbage incinerator 03; The grate 03 composes the drying section grate 201, the combustion section grate 202 and the incineration section furnace according to the "overlapping method of fixed grate, sliding grate, fixed grate, sliding grate...Finally discharging grate" Row 203. From high to low, set up end to end to form a hearth. The drying grate 201 and the combustion grate 202 are inclined at an angle of 20° to the horizontal; the ember grate 203 is arranged horizontally, which can reduce the heat reduction rate of the slag; the grate block material is made of high chromium cast steel; the grate system The drying section grate 201, the combustion section grate 202 and the ember section grate 203 are each driven by an independent drive mechanism,...
PUM
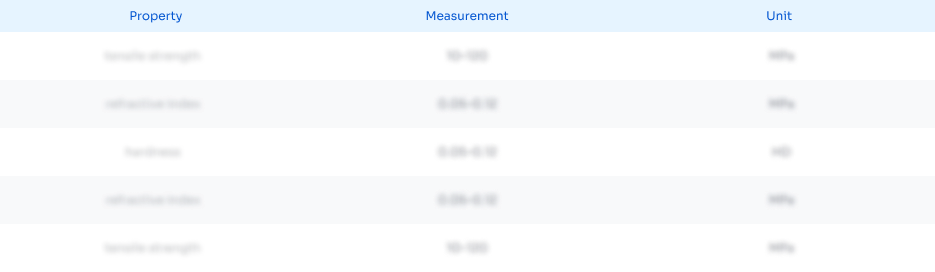
Abstract
Description
Claims
Application Information

- Generate Ideas
- Intellectual Property
- Life Sciences
- Materials
- Tech Scout
- Unparalleled Data Quality
- Higher Quality Content
- 60% Fewer Hallucinations
Browse by: Latest US Patents, China's latest patents, Technical Efficacy Thesaurus, Application Domain, Technology Topic, Popular Technical Reports.
© 2025 PatSnap. All rights reserved.Legal|Privacy policy|Modern Slavery Act Transparency Statement|Sitemap|About US| Contact US: help@patsnap.com