A kind of oil-resistant coated white cardboard and its production process
A technology of cloth white cardboard and production process, applied in the field of papermaking, can solve problems such as hidden dangers and contaminate food safety, and achieve the effects of high oil resistance, reduced production cost and easy realization.
- Summary
- Abstract
- Description
- Claims
- Application Information
AI Technical Summary
Problems solved by technology
Method used
Image
Examples
Embodiment 1
[0056] Surface layer pulp: wood pulp (percentage by weight: 80% bleached hardwood kraft pulp, 20% bleached softwood kraft pulp), crushed and mixed by a pulper, refined by a disc refiner, and enter the surface of the paper machine net filter.
[0057] Core layer pulp: wood pulp (weight percentage: 70% bleached chemical thermomechanical pulp, 30% broken paper), crushed and mixed by a pulper, refined by a disc refiner, and filtered into the paper machine core net.
[0058] Bottom pulp: wood pulp (percentage by weight: 75% bleached hardwood kraft pulp, 25% bleached softwood kraft pulp), disintegrated and mixed by a pulper, refined by a disc refiner, and enter the surface wire of the paper machine filter.
[0059] Then, a three-layer laminated wire is formed by a paper machine to produce a wet paper sheet with a surface layer 103, a core layer 102 and a bottom layer 101. The wet paper sheet is dried by a paper machine and the surface is sized to obtain a base paper.
[0060] Then...
Embodiment 2
[0068] The production process of this embodiment is the same as that of the above-mentioned embodiment 1, the difference lies in: the slurry ratio of the surface layer slurry, the core layer slurry, and the bottom layer slurry, and the coating ratio of the back-coated oil-proof layer.
[0069] Surface layer size (percentage by weight): 95% of bleached hardwood kraft pulp, 5% of bleached softwood kraft pulp;
[0070] Core layer pulp (percentage by weight): bleached chemical thermomechanical pulp 65%, broken paper 35%;
[0071] Bottom pulp (percentage by weight): 85% of bleached hardwood kraft pulp, 15% of bleached softwood kraft pulp;
[0072] The coating ratio of the back-coated oil-proof layer is (parts by weight): 100 parts of pigment are mixed with calcium carbonate and china clay, 50 parts of calcium carbonate and china clay, 75 parts of latex, 0.6 part of carboxymethyl cellulose, and 0.12 part of dispersant , 1 part of anti-water agent, 1.2 parts of lubricant, 0.035 part...
Embodiment 3
[0078] Surface layer size (percentage by weight): 90% of bleached hardwood kraft pulp, 10% of bleached softwood kraft pulp;
[0079] Core layer pulp (percentage by weight): bleached chemical thermomechanical pulp 75%, broken paper 25%;
[0080] Bottom pulp (percentage by weight): 80% of bleached hardwood kraft pulp, 20% of bleached softwood kraft pulp;
[0081] The coating ratio of the back-coated oil-repellent layer is (parts by weight): 100 parts of pigments are all composed of china clay, that is, 100 parts of china clay, 100 parts of latex, 0.3 part of carboxymethyl cellulose, 0.08 part of dispersant, and 0.7 part of water repellent part, 0.8 part of lubricant, 0.035 part of defoamer, 0.12 part of caustic soda, and 0.18 part of fungicide.
[0082] The coating amounts of the precoat layer 104, the core coat layer 105, and the top coat layer 106 were 9 g / m2, 11 g / m2, and 11 g / m2, respectively.
[0083] The produced oil-proof coated white cardboard is compared with the same...
PUM
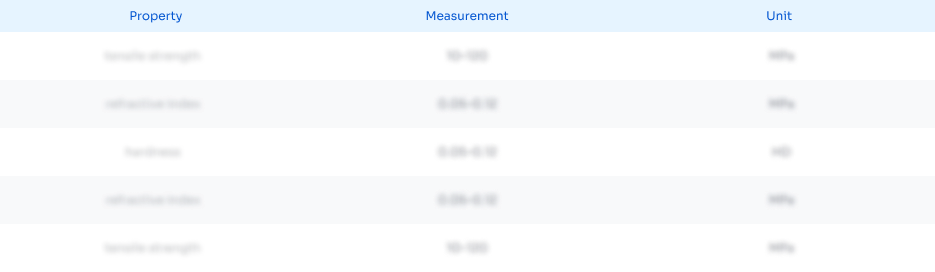
Abstract
Description
Claims
Application Information

- R&D
- Intellectual Property
- Life Sciences
- Materials
- Tech Scout
- Unparalleled Data Quality
- Higher Quality Content
- 60% Fewer Hallucinations
Browse by: Latest US Patents, China's latest patents, Technical Efficacy Thesaurus, Application Domain, Technology Topic, Popular Technical Reports.
© 2025 PatSnap. All rights reserved.Legal|Privacy policy|Modern Slavery Act Transparency Statement|Sitemap|About US| Contact US: help@patsnap.com