Sheet material hydro-mechanical deep drawing forming device and method using magnetic medium to pressurize
A technology of liquid-filled deep drawing and medium, applied in the field of liquid-filled deep drawing, which can solve the problems of reduced overflow pressure in the flange area, uniformity of wrinkling deformation, etc.
- Summary
- Abstract
- Description
- Claims
- Application Information
AI Technical Summary
Problems solved by technology
Method used
Image
Examples
specific Embodiment approach 1
[0018] Specific implementation mode one: as Figure 1~2 As shown, the liquid-filled deep-drawing forming device for sheet materials pressurized by a magnetic medium in this embodiment includes a punch 1, a die 2, a blank holder 3, a lower plunger 4, a first coil 6, and a second coil 7 And the magnetic control unit 8; the blank holder 3 is located on the die 2, the closed liquid chamber 5 formed by the die 2 and the lower plunger 4 is used to accommodate the magnetic medium, and the punch 1 can pass through the blank holder 3 Drive the slab 9 down to enter the closed liquid chamber 5 formed by the die 2 and the lower plunger 4, the first coil 6 is arranged around the outside of the flange area 10 formed by the die 2 and the blank holder 3, The second coil 7 is arranged on the pull rod of the lower plunger 4, and the magnetic control unit 8 is used to control the magnitude of the magnetic field generated by the first coil 6 and the second coil 7, and then respectively control th...
specific Embodiment approach 2
[0019] Specific implementation mode two: as Figure 1~2 As shown, this embodiment is a sheet material liquid-filled deep drawing method using the magnetic medium pressurization of the forming device described in Embodiment 1, and the method is realized according to the following steps;
[0020] Step 1. Prepare the required magnetic medium in fluid-solid coupling state, and control its solid phase ratio to 50% to 80%; Step 2. Control the initial position of the working end face of the lower plunger 4: the working end face of the lower plunger 4 The distance from the upper end surface of the die 2 is one-third of the total depth H of the die; step 3, filling the closed liquid chamber cavity 5 formed by the die 2 and the lower plunger 4 with the above-mentioned magnetic medium; step 4. Place the slab 9 on the upper end surface of the die 2; step 5, move the blank holder 3 down to the slab 9; step 6, use the magnetic control unit 8 to control the second coil 7 at the lower plunger...
specific Embodiment approach 3
[0022] Embodiment 3: The magnetic medium in step 1 of this embodiment is composed of 7 parts of carbonyl iron powder, 2 parts of synthetic oil or ethylene glycol, and 1 part of surfactant according to the ratio of parts by mass. Other steps are the same as in the second embodiment. The viscosity degree caused by the distribution state of the magnetic medium of such components under the action of a magnetic field is more conducive to regulation. If the solid phase rate (carbonyl iron powder content) is too high, it will not be able to achieve "" "soft" back pressure; if the solid phase ratio (carbonyl iron powder) is too low, it is difficult to achieve the effect of increasing the overflow pressure at the blank holder. The magneto-inductive medium of the above-mentioned components makes the effect of "flexible" back pressure and the effect of overflow pressure at the blank holder optimal.
PUM
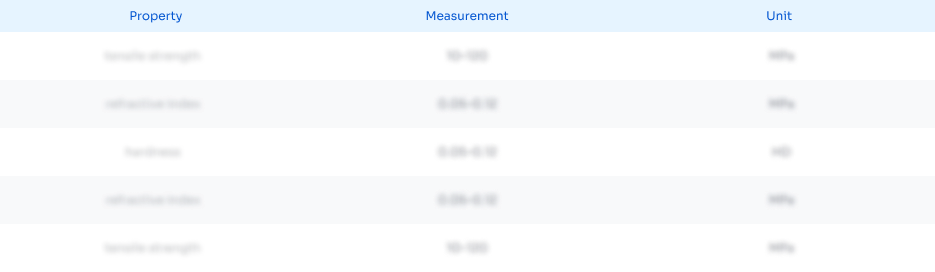
Abstract
Description
Claims
Application Information

- R&D
- Intellectual Property
- Life Sciences
- Materials
- Tech Scout
- Unparalleled Data Quality
- Higher Quality Content
- 60% Fewer Hallucinations
Browse by: Latest US Patents, China's latest patents, Technical Efficacy Thesaurus, Application Domain, Technology Topic, Popular Technical Reports.
© 2025 PatSnap. All rights reserved.Legal|Privacy policy|Modern Slavery Act Transparency Statement|Sitemap|About US| Contact US: help@patsnap.com