Hot-working process capable of improving cogging for titanium alloy cast ingot
A titanium alloy and hot working technology, which is applied in the field of improving the hot working process of titanium alloy ingot blanking, can solve the problems of unstable head shrinkage hole depth, large amount of shrinkage hole removal, surface cracking, etc., so as to eliminate end face shrinkage. The effect of hole phenomenon, good surface quality and improved product yield
- Summary
- Abstract
- Description
- Claims
- Application Information
AI Technical Summary
Problems solved by technology
Method used
Examples
Embodiment 1
[0020] Step 1. Peel the Ф690mm TC11 ingot smelted in a vacuum consumable electric arc furnace, cut off the riser, and then remove the surface defects of the ingot by grinding;
[0021] Step 2. Place the TC11 ingot from which surface defects have been removed in step 1 in a heating furnace, preheat it at 800°C for 1.5 hours, then raise the temperature to 180°C above the β-transition point of the ingot, and keep it warm for 380 minutes;
[0022] Step 3. Place the TC11 ingot after heat preservation in step 2 on a 2500T hydraulic press with an anvil width of 350mm, and carry out billet forging at an initial forging temperature of 100°C to 150°C above the β phase transition point of the ingot, and control the final Forging temperature ≥ 850 ℃, blank forging process is:
[0023] 301. Start pressing from the middle of the ingot to the opposite direction of the jaws, control the feed rate of each pass to 300mm, and the reduction amount of each pass to 100mm. When pressing to a distanc...
Embodiment 2
[0029] Step 1. Peel the Ф790mm TC4 ingot smelted in a vacuum consumable electric arc furnace, cut off the riser, and then remove the surface defects of the ingot by grinding;
[0030] Step 2. Place the TC4 ingot from which surface defects have been removed in step 1 in a heating furnace, preheat for 2.5 hours at a temperature of 750°C, then raise the temperature to 150°C above the β-transition point of the ingot, and keep it warm for 425 minutes;
[0031] Step 3. Place the TC4 ingot after heat preservation in step 2 on a 2500T hydraulic press with an anvil width of 350mm, carry out billet forging at an initial forging temperature of 100°C to 150°C above the β phase transition point of the ingot, and control the final Forging temperature ≥ 850 ℃, blank forging process is:
[0032] 301. Start pressing from the middle of the ingot to the opposite direction of the jaws, control the feed rate of each pass to 330mm, and the reduction amount of each pass to 120mm. When pressing to a ...
Embodiment 3
[0038] Step 1. Peel the Ф690mm TC6 ingot smelted in a vacuum consumable electric arc furnace, cut off the riser, and then remove the surface defects of the ingot by grinding;
[0039] Step 2. Place the TC6 ingot from which surface defects have been removed in step 1 in a heating furnace, preheat it at a temperature of 780°C for 2 hours, then raise the temperature to 200°C above the β phase transition point of the ingot, and keep it warm for 405 minutes;
[0040] Step 3. Place the TC6 ingot after heat preservation in step 2 on a 2500T hydraulic press with an anvil width of 300mm, carry out billet forging at an initial forging temperature of 100°C to 150°C above the β phase transition point of the ingot, and control the final Forging temperature ≥ 850 ℃, blank forging process is:
[0041] 301. Press down in turn from the middle of the ingot to the opposite direction of the jaws, control the feed rate of each pass to 280mm, and the reduction amount per pass to 95mm. When the ingo...
PUM
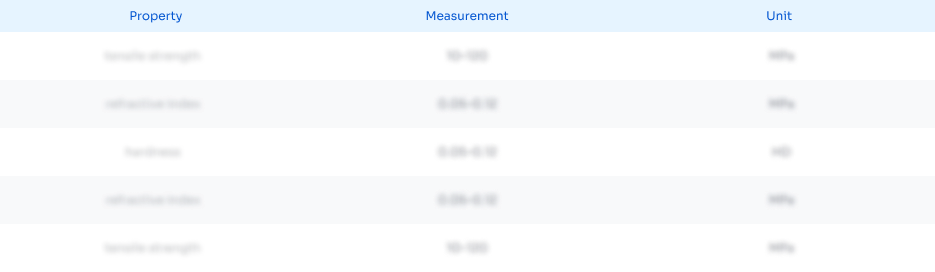
Abstract
Description
Claims
Application Information

- R&D
- Intellectual Property
- Life Sciences
- Materials
- Tech Scout
- Unparalleled Data Quality
- Higher Quality Content
- 60% Fewer Hallucinations
Browse by: Latest US Patents, China's latest patents, Technical Efficacy Thesaurus, Application Domain, Technology Topic, Popular Technical Reports.
© 2025 PatSnap. All rights reserved.Legal|Privacy policy|Modern Slavery Act Transparency Statement|Sitemap|About US| Contact US: help@patsnap.com