Hydraulic superhigh-frequency vibrating power head
A power head, ultra-high frequency technology, applied in drilling equipment, drilling equipment and methods, impact drilling and other directions, can solve the problems of shallow drilling depth, low vibration frequency, poor formation adaptability, etc. Synchronized operation, improve work efficiency, increase drilling speed and sampling depth effect
- Summary
- Abstract
- Description
- Claims
- Application Information
AI Technical Summary
Problems solved by technology
Method used
Image
Examples
Embodiment 1
[0017] figure 1 Schematically shows the structure of the preferred embodiment of the present invention, as shown in the figure, this preferred embodiment includes a rotary motor 1, a coupling 2, a coupling box 3, a power head back plate 4, a main shaft 5, a vibration Vibrator 9, vibration damping device and supporting plate 10, rotary motor 1 is connected with the upper end of the main shaft 5 through the coupling 2, the main shaft runs through the vibrator 9 up and down, and the lower end of the main shaft 5 is connected with the drill pipe and the drilling tool (not shown in the figure) . The vibrator 9 is connected with the base plate of the shaft coupling box 3 through a damping device, and the power head back plate 4 is connected to the chain back plate of the rig mast, and can slide up and down on the rig mast to achieve the purpose of drilling and lifting the drill. The supporting plate 10 plays a safety role, preventing the vibrator from falling suddenly and causing ...
Embodiment 2
[0020] In embodiment 2, other structures are all identical with embodiment 1 structure, and difference is:
[0021] The synchronous belt / synchronous wheel forced synchronization mechanism is placed on the side close to the power head back plate 4, including the synchronous wheel 21, the guide wheel 24, the pressing wheel 23 and the synchronous belt 22, and the synchronous belt / synchronous wheel forced synchronous mechanism can ensure two The rotational speeds of the eccentric shaft 16 are completely synchronized to better realize self-synchronous operation.
Embodiment 3
[0023] In Embodiment 3, other structures are the same as those in Embodiment 2, except that the high-speed bearing cooling and lubricating mechanism includes an oil cup 13 , an air filter 15 and an air suction impeller 17 . Grease is injected through the oil cup 13 to lubricate the high-speed bearing 14 , and the eccentric shaft 16 drives the suction impeller 17 to rotate at a high speed to inhale air to air-cool the high-speed bearing 14 .
PUM
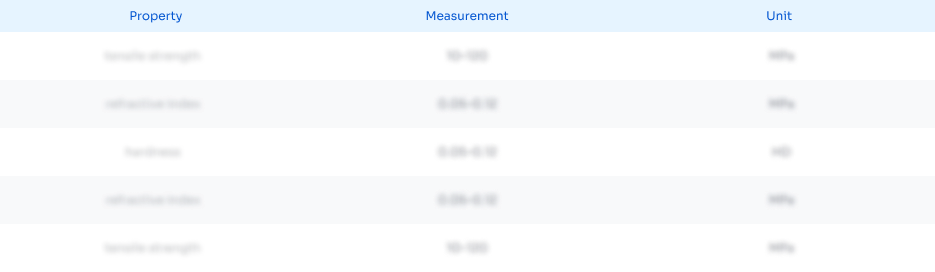
Abstract
Description
Claims
Application Information

- R&D
- Intellectual Property
- Life Sciences
- Materials
- Tech Scout
- Unparalleled Data Quality
- Higher Quality Content
- 60% Fewer Hallucinations
Browse by: Latest US Patents, China's latest patents, Technical Efficacy Thesaurus, Application Domain, Technology Topic, Popular Technical Reports.
© 2025 PatSnap. All rights reserved.Legal|Privacy policy|Modern Slavery Act Transparency Statement|Sitemap|About US| Contact US: help@patsnap.com