Preparation method of urea-phenol-formaldehyde resin adhesive used for E0 grade solid wood composite floorboard
A technology of solid wood composite flooring and formaldehyde resin, which is applied to floors, buildings, building structures, etc., can solve the problems of complex operation and high processing cost, and achieve the effect of simple glue making process, good reproducibility, and easy control of operation
- Summary
- Abstract
- Description
- Claims
- Application Information
AI Technical Summary
Problems solved by technology
Method used
Image
Examples
Embodiment 1
[0026] an E 0 The preparation method of urea-phenol-formaldehyde resin glue for solid wood composite flooring,
[0027] Step 1: Add 95.4g of phenol, 100g of the first batch of 36.5wt% formaldehyde solution, 38g of the first batch of urea, 10g of water and 0.3g of CaO into a 500ml four-necked flask, and heat up to 90°C for 40min.
[0028] The second step: add the second batch of 36.5wt% formaldehyde solution 107g, the second batch of urea 38g, gradually add 30wt% NaOH solution 15g, react at 88-90°C for 70min.
[0029] The third step: add the third batch of 36.5wt% formaldehyde solution 8g, gradually add the second batch of 30wt% NaOH solution 20g, react at 85-90°C for 60min.
[0030] Step 4: Add the third batch of urea 15g, the third batch of 30wt% NaOH solution 35g, react at 80-85°C for 35min, the viscosity is 1.6s, cool and discharge.
[0031] Test its physical and chemical properties, and the results are listed in Attached Table 1. Press poplar plywood to test the bonding ...
Embodiment 2
[0033] an E 0 The preparation method of urea-phenol-formaldehyde resin glue for solid wood composite flooring,
[0034] Step 1: Add 95.4g of phenol, 110g of the first batch of 36.5wt% formaldehyde solution, 45g of the first batch of urea, 10g of water and 0.3g of CaO into a 500ml four-neck flask, and heat up to 92°C for 40min.
[0035] The second step: add the second batch of 36.5wt% formaldehyde solution 117g, the second batch of urea 45g, gradually add 30wt% NaOH solution 15g, react at 91°C for 60min.
[0036] The third step: add the third batch of 36.5wt% formaldehyde solution 8g, gradually add the second batch of 30wt% NaOH solution 20g, react at 85-90°C for 60min.
[0037] Step 4: Add the third batch of urea 15g, the third batch of 30wt% NaOH solution 35g, react at 80-85°C for 20min, the viscosity is 1.6s, cool and discharge.
[0038] Test its physical and chemical properties, and the results are listed in Attached Table 1. Press poplar plywood to test the bonding stren...
Embodiment 3
[0041] an E 0 The preparation method of urea-phenol-formaldehyde resin glue for solid wood composite flooring,
[0042] Step 1: Add 76.8g of phenol, 90g of the first batch of 36.5wt% formaldehyde solution, 42g of the first batch of urea, 9g of water and 0.3g of CaO into a 500ml four-neck flask, and heat up to 88°C for 50min.
[0043] The second step: add the second batch of 36.5wt% formaldehyde solution 110g, the second batch of urea 42g, gradually add 30wt% KOH solution 15g, react at 89-91°C for 70min.
[0044] The third step: add the third batch of 36.5wt% formaldehyde solution 5g, gradually add the second batch of 30wt% KOH solution 20g, react at 85-90°C for 60min.
[0045] Step 4: Add the third batch of urea 12g, the third batch of 30wt% KOH solution 35g, react at 80-85°C for 10min, the viscosity is 1.6s, cool and discharge.
[0046] Test its physical and chemical properties, and the results are listed in Attached Table 1. Press poplar plywood to test the bonding strengt...
PUM
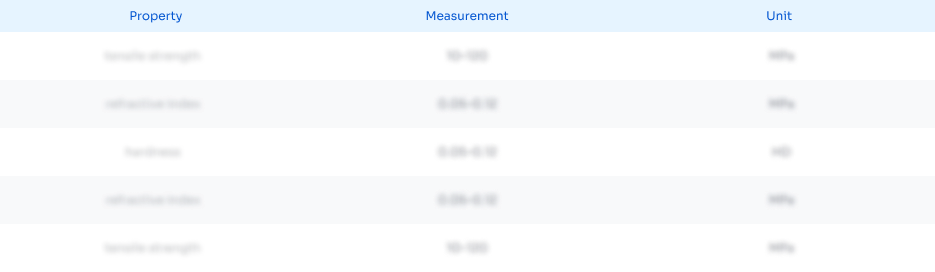
Abstract
Description
Claims
Application Information

- R&D Engineer
- R&D Manager
- IP Professional
- Industry Leading Data Capabilities
- Powerful AI technology
- Patent DNA Extraction
Browse by: Latest US Patents, China's latest patents, Technical Efficacy Thesaurus, Application Domain, Technology Topic, Popular Technical Reports.
© 2024 PatSnap. All rights reserved.Legal|Privacy policy|Modern Slavery Act Transparency Statement|Sitemap|About US| Contact US: help@patsnap.com