Synthetic method of monomethyl adipate
A technology of monoethyl adipate and synthesis method, which is applied in the field of synthesis of monoethyl adipate, can solve problems such as unstable chemical properties of adipic anhydride, easily corroded equipment, and pollute the environment, and achieve convenient post-processing, Resource saving and high yield effect
- Summary
- Abstract
- Description
- Claims
- Application Information
AI Technical Summary
Problems solved by technology
Method used
Image
Examples
Embodiment 1
[0029] A) Resin pretreatment, first soak the styrene-based macroporous cation exchange tree in the order of acid solution soaking, alkali solution soaking and acid solution soaking again, and rinse with deionized water after each soaking, specifically: First soak the styrene macroporous cation exchange resin with a hydrochloric acid solution with a mass percentage concentration of 3%, wherein the weight ratio of the hydrochloric acid solution with a mass percentage concentration of 3% to the styrene macroporous cation exchange resin is 5:1 , soaking time is 150min, drain the hydrochloric acid solution after the soaking is over, i.e. drain the acid solution and rinse with deionized water to pH7, then use a sodium hydroxide solution with a mass percentage concentration of 3% for soaking, the sodium hydroxide solution and The weight ratio of styrene-based macroporous cation exchange resin is 5: 1, and the soaking time of alkali solution is 150min. After soaking in alkali solution,...
Embodiment 2
[0032] A) Resin pretreatment, be that the hydrochloric acid solution of 5% with mass percentage concentration is soaked to styrene series macroporous cation exchange resin earlier, wherein mass percentage concentration is the hydrochloric acid solution of 5% and styrene series macroporous cation exchange resin The weight ratio is 4:1, and the soaking time is 210min. After the soaking, the hydrochloric acid solution is exhausted, that is, the acid solution is exhausted and the acid solution is rinsed with deionized water to pH5, and then soaked in a sodium hydroxide solution with a mass percentage concentration of 5%. The weight ratio of this sodium hydroxide solution and styrene series macroporous cation exchange resin is 4: 1, and the time of lye soaking is 210min, and after lye immersion is finished, the sodium hydroxide solution is exhausted and the lye is exhausted, and again Rinse with deionized water to pH 7, then soak again for 210 minutes with 5% hydrochloric acid solut...
Embodiment 3
[0035] A) Resin pretreatment, be that the hydrochloric acid solution of 4% is soaked to styrene series macroporous cation exchange resin with mass percent concentration earlier, wherein mass percent concentration is the hydrochloric acid solution of 4% and styrene series macroporous cation exchange resin The weight ratio is 3:1, and the soaking time is 180min. After soaking, the hydrochloric acid solution is exhausted, that is, the acid solution is drained and the pH is rinsed with deionized water to pH6, and then soaked in a sodium hydroxide solution with a mass percentage concentration of 4%. The weight ratio of this sodium hydroxide solution and styrene series macroporous cation exchange resin is 3: 1, and the time of lye soaking is 180min, and after lye immersion is finished, the sodium hydroxide solution is exhausted and the lye is exhausted, and again Rinse with deionized water to pH 8, and then soak for 180 minutes again with a hydrochloric acid solution with a concentra...
PUM
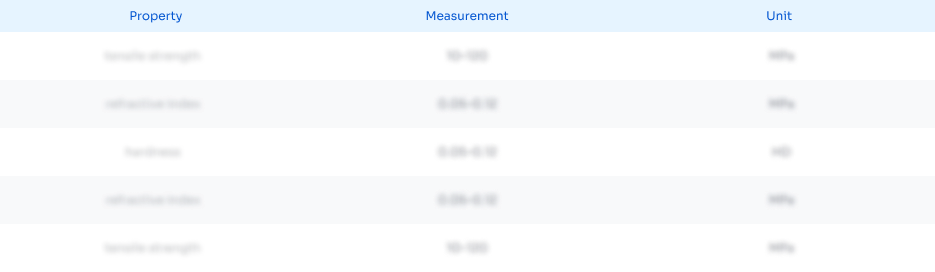
Abstract
Description
Claims
Application Information

- R&D
- Intellectual Property
- Life Sciences
- Materials
- Tech Scout
- Unparalleled Data Quality
- Higher Quality Content
- 60% Fewer Hallucinations
Browse by: Latest US Patents, China's latest patents, Technical Efficacy Thesaurus, Application Domain, Technology Topic, Popular Technical Reports.
© 2025 PatSnap. All rights reserved.Legal|Privacy policy|Modern Slavery Act Transparency Statement|Sitemap|About US| Contact US: help@patsnap.com