Processing technology for disc-type brake lining
A disc brake and processing technology, which is applied to household components, household appliances, other household appliances, etc., can solve the problems of unstable disc brake lining structure and low processing efficiency, and improve convenience and safety. effect of improving safety
- Summary
- Abstract
- Description
- Claims
- Application Information
AI Technical Summary
Problems solved by technology
Method used
Image
Examples
Embodiment Construction
[0015] See attached figure 1 with attached figure 2 , the processing technology of the disc brake lining disclosed in the present invention includes the processing equipment of the disc brake lining. Slidable upper sliding seat 2, middle sliding seat 3 and lower sliding seat 4, and upper sliding seat driving mechanism 5, middle sliding seat driving mechanism 6 and The lower seat drive mechanism 7, the lower seat 4 is provided with a workbench 8, the workbench 8 is provided with a steel-backed carriage 9 for placing disc brake linings, and the middle slide 3 is provided with There is a middle mold body 10 that can slide up and down with the middle sliding seat 3. The middle mold body 10 is provided with a number of friction lining forming cavities for disc brake linings that are transparent up and down. The upper sliding seat 2 corresponds to One side of the middle mold body 10 is provided with an upper mold body 11 that can slide up and down with the upper slide seat 2. The...
PUM
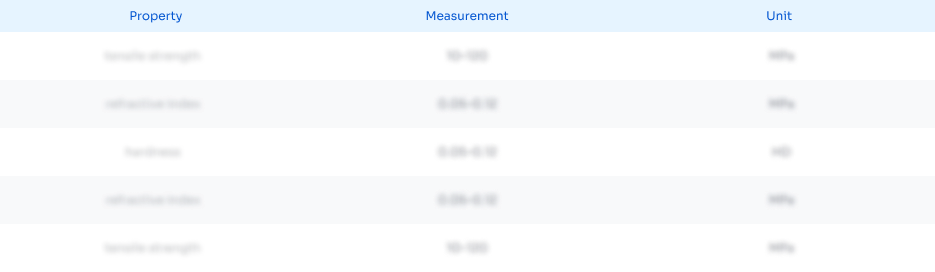
Abstract
Description
Claims
Application Information

- R&D Engineer
- R&D Manager
- IP Professional
- Industry Leading Data Capabilities
- Powerful AI technology
- Patent DNA Extraction
Browse by: Latest US Patents, China's latest patents, Technical Efficacy Thesaurus, Application Domain, Technology Topic, Popular Technical Reports.
© 2024 PatSnap. All rights reserved.Legal|Privacy policy|Modern Slavery Act Transparency Statement|Sitemap|About US| Contact US: help@patsnap.com