Deep level ion nitriding process for engine cylinder bushes
An engine cylinder, ion nitriding technology, applied in the direction of metal material coating process, coating, solid diffusion coating, etc., to achieve the effect of deep nitriding layer, reducing heat dissipation speed, and fast nitriding speed
- Summary
- Abstract
- Description
- Claims
- Application Information
AI Technical Summary
Problems solved by technology
Method used
Image
Examples
Embodiment Construction
[0018] It is suitable for the deep ion nitriding process of the engine cylinder liner. The material of the cylinder liner is 38CrMoAlA. The surface hardness of the cylinder liner after nitriding is ≥80HRA, and the surface hardness of the finished cylinder liner is ≥76HRA; the brittleness of the nitrided layer is level 1; The depth of the nitriding layer is 0.52-0.80mm, the depth of the nitriding layer of the finished cylinder liner is 0.3-0.6mm; the size deviation of the inner hole after nitriding is required to be within 0.09 mm, and the inner hole size of the cylinder liner after nitriding in this embodiment requires φ149.68 -φ149.77mm.
[0019] The nitriding equipment is LDMC-150 pulse power glow ion nitriding furnace, which can output 0-1000V continuously adjustable voltage. The effective working size of the furnace body is φ1200×1300mm. The heat shield is made of stainless steel, and the outer heat shield is made of aluminum alloy. The vacuum in the furnace is measured w...
PUM
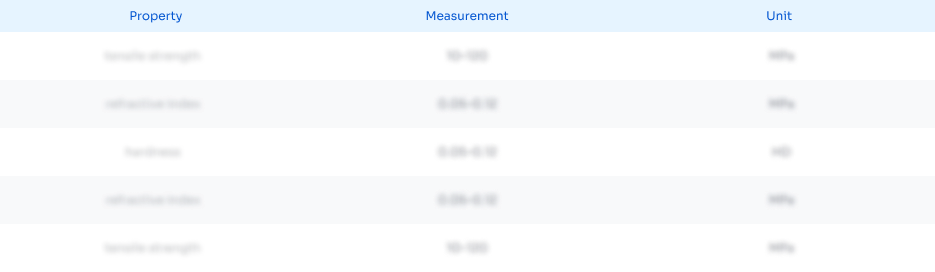
Abstract
Description
Claims
Application Information

- R&D
- Intellectual Property
- Life Sciences
- Materials
- Tech Scout
- Unparalleled Data Quality
- Higher Quality Content
- 60% Fewer Hallucinations
Browse by: Latest US Patents, China's latest patents, Technical Efficacy Thesaurus, Application Domain, Technology Topic, Popular Technical Reports.
© 2025 PatSnap. All rights reserved.Legal|Privacy policy|Modern Slavery Act Transparency Statement|Sitemap|About US| Contact US: help@patsnap.com