Method for preparing dual-molecular-sieve-containing cracking catalyst by using in-situ crystallization
A cracking catalyst and bimolecular sieve technology, which is applied in molecular sieve catalysts, physical/chemical process catalysts, catalytic cracking, etc., can solve the problems that the preparation of in-situ crystallization has not been published, and the pellet catalyst cannot meet the requirements of fluidized operation, etc. , to achieve the effect of rich catalyst pores and strong conversion ability of heavy oil
- Summary
- Abstract
- Description
- Claims
- Application Information
AI Technical Summary
Problems solved by technology
Method used
Image
Examples
Embodiment 1
[0029] With 80 grams of NaZSM-5 molecular sieve (industrial product, Leshan Runhe Catalytic New Material Co., Ltd., silicon-aluminum ratio 30), 80 grams of NaY molecular sieve (same as above, silicon-aluminum ratio 5.0, crystallinity 90%), 800 grams of kaolin and 3 liters of water Add to beating in the gel-forming kettle for 30 minutes, add 400 milliliters of silica sol (same as above, SiO 2 25% by weight) after continuing beating for 30 minutes, use a high-shear mixing emulsifier (MBE-100L type, manufactured by Shanghai Environmental Protection Equipment General Factory) beating and homogenizing after 30 minutes in the laboratory with a small spray dryer (LPG-5 type, Changzhou Jianda Drying Equipment Co., Ltd.) is made into the microsphere of embodiment 1, and its average particle diameter is 65 microns.
[0030] Roast the microspheres at 200° C. for 2 hours to dehydrate in a calciner system with an air pump at a pressure of 0.05 MPa, then turn off the air pump and open the ...
Embodiment 2
[0037] Add 40 grams of HZSM-5 molecular sieve (same as above, silicon-aluminum ratio of 50), 40 grams of HY molecular sieve (same as above, silicon-aluminum ratio of 6.5, crystallinity 80%), 850 grams of kaolin and 3 liters of water into the gelling kettle for beating for 30 minutes, Add 200 ml aluminum sol (same as above, SiO 2 20% by weight), 150 grams of pseudo-boehmite (industrial product, Shanxi Aluminum Plant of Aluminum Corporation of China, solid content 65% by weight) and 25 milliliters of hydrochloric acid (chemically pure, Beijing Chemical Reagent Company, 33% by weight) continue beating for 40 Minutes later, beating and homogenizing with a high-shear mixing emulsifier (same as above) after 30 minutes, the microspheres of embodiment 2 were made on a small spray dryer (same as above) in the laboratory, and its average particle diameter was 62 microns.
[0038] Roast the microspheres at 300° C. for 1 hour to dehydrate in a roasting furnace system with an air pump at ...
Embodiment 3
[0043] 40 g NH 4 ZSM-5 molecular sieve (the same, silicon-aluminum ratio 50) and 40 grams of rare earth ZSM-5 molecular sieve (the same, silicon-aluminum ratio 30, rare earth oxide 2.0% by weight), 40 grams of NH 4 Y molecular sieve (same as above, silicon-aluminum ratio 5.0, crystallinity 90%), 40 grams of rare earth USY molecular sieve (same as above, 2.0 weight percent of rare earth oxide), 850 grams of kaolin and 3 liters of water are added to the gelling kettle for beating for 30 minutes, and 400 ml Sodium silicate (same as above) continues beating after 40 minutes, with high-shear mixing emulsifying machine (same as above) beating homogeneously after 30 minutes, the microsphere of embodiment 3 is made on the small-sized spray drier (same as above) in laboratory, its The average particle diameter is 64 microns.
[0044] Roast the microspheres at 350° C. for 1 hour to dehydrate in a calciner system with an air pump at a pressure of 0.06 MPa, then turn off the air pump and...
PUM
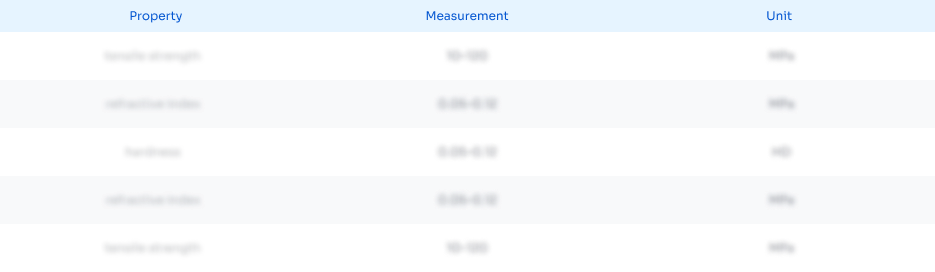
Abstract
Description
Claims
Application Information

- R&D
- Intellectual Property
- Life Sciences
- Materials
- Tech Scout
- Unparalleled Data Quality
- Higher Quality Content
- 60% Fewer Hallucinations
Browse by: Latest US Patents, China's latest patents, Technical Efficacy Thesaurus, Application Domain, Technology Topic, Popular Technical Reports.
© 2025 PatSnap. All rights reserved.Legal|Privacy policy|Modern Slavery Act Transparency Statement|Sitemap|About US| Contact US: help@patsnap.com