Novel positioning compensation method for PCB by single vision camera
A compensation method and a single-camera technology, applied to measuring devices, instruments, and optical devices, can solve the problems that the mechanical positioning accuracy cannot meet customer requirements, and achieve the effects of improving competitive advantages, high precision, and convenient use
- Summary
- Abstract
- Description
- Claims
- Application Information
AI Technical Summary
Problems solved by technology
Method used
Image
Examples
Embodiment Construction
[0029] one. basic method:
[0030] 1, Basic guarantee: We guarantee that the machine table should have assembly relationship and precision, and the linear drive of motion. Such as: the right angle of the XY platform, the installation of the laser is correct (including the level and parallel to the platform). For specific methods, refer to technical documents: and
[0031] 2. Compensation improves accuracy: The calculation method of CCD compensation is scientific and reasonable. Currently: a single camera captures two to three positioning points, calculates the current position of the board, and makes compensation.
[0032] (1). Coordinate system learning: The machine has three basic coordinate systems, one is the XY-A platform, the other is the base map of the PCB-B board, and the third is the graphic position of the laser L-C. CCD is a fixed eye position (Xz, Yz) in the A coordinate system, such as image 3 shown.
[0033] (2). Compensation method:
[0034] a. As ...
PUM
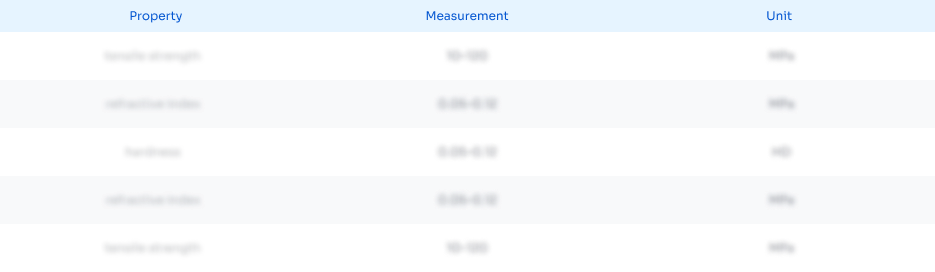
Abstract
Description
Claims
Application Information

- R&D
- Intellectual Property
- Life Sciences
- Materials
- Tech Scout
- Unparalleled Data Quality
- Higher Quality Content
- 60% Fewer Hallucinations
Browse by: Latest US Patents, China's latest patents, Technical Efficacy Thesaurus, Application Domain, Technology Topic, Popular Technical Reports.
© 2025 PatSnap. All rights reserved.Legal|Privacy policy|Modern Slavery Act Transparency Statement|Sitemap|About US| Contact US: help@patsnap.com