Staining method for wet spinning of acrylic fibers
A technology of wet spinning and acrylic fiber, which is applied in the field of step-by-step coloring of wet spinning, can solve the problems of low color fastness, low pigment concentration, large amount of addition, etc., and achieves cumbersome process operation, easy coloring, colorful effect
- Summary
- Abstract
- Description
- Claims
- Application Information
AI Technical Summary
Problems solved by technology
Method used
Examples
Embodiment 1
[0033] According to the weight ratio of the following materials, cationic dye 0.01%, acetic acid (concentration 98%) 0.5%, leveling agent Pingpingjia-O (ie Peregal-O, fatty alcohol polyoxyethylene ether) 0.05%, deionized water 99.44% , prepared into a dye bath with a pH of 6.0 for use; immerse the modified polyacrylonitrile raw material in the above dye bath, and adopt the temperature control method for dyeing, the dyeing starting temperature is set at 50°C, and the temperature is raised at a heating rate of 0.5°C / min to 80°C, heat-dye for 15 minutes, then heat up to 90°C at a rate of 0.1°C / min, heat-dye for 20 minutes, heat up to 100°C and then boil for 45 minutes, and finally slowly drop to 50°C within 20 minutes, and the modified The polyacrylonitrile raw material was taken out, washed with water, and then dried in an oven at 80°C for use.
[0034] Add 0.3w% polyurethane type polymer dispersant, 0.1w% dustproof agent fumed silica and 0.1w% matting agent superfine silica to ...
Embodiment 2
[0037] The following materials are prepared by weight ratio, cationic dye 2%, acetic acid (98%) 1%, leveling agent Pingpingjia-O 0.5%, deionized water 96.5%, and are prepared into a dye bath with a pH of 6.5 for use; Immerse the modified polyacrylonitrile raw material in the above-mentioned dyeing bath, and use the controlled temperature rise method to dye. The dyeing starting temperature is set at 70°C, and the temperature is raised to 85°C at a heating rate of 1°C / min, kept for 30 minutes and dyed at 0.5°C Heat up to 95°C at a rate of 1 / min, keep warm for 30 minutes, heat up to 100°C and then boil for 50 minutes, and finally slowly drop to 50°C within 25 minutes, take out the modified polyacrylonitrile raw material obtained by exhaust dyeing, wash it with water and place it at 95°C Oven dry for later use.
[0038]Add the polyurethane type macromolecular dispersant of 3w%, the dustproof agent modified hydrogenated castor oil of 0.5w% and the matting agent talcum powder of 1w%...
Embodiment 3
[0041] Prepare the following materials by weight ratio, cationic dye 5%, acetic acid (98%) 2%, leveling agent Pingpingjia-O2%, deionized water 92%, and prepare a dye bath with a pH of 7 for use; the modified The polyacrylonitrile raw material is immersed in the above-mentioned dyeing bath, and is dyed by the controlled temperature rise method. The dyeing starting temperature is set at 80°C, and the temperature is raised to 90°C at a heating rate of 2°C / min. Raise the temperature to 95°C, keep warm for 60 minutes, heat up to 100°C and boil for 60 minutes, and finally drop to 50°C slowly within 30 minutes, take out the modified polyacrylonitrile raw material obtained by exhaust dyeing, wash it with water, and dry it in an oven at 110°C stand-by.
[0042] Add 8w% of polyurethane polymer dispersant, 2w% of N-methylpyrrolidone solution of dustproof agent modified polyurea and 2w% of matting agent titanium dioxide into the stirring tank, and add 73w% of solvent dimethyl Sulfoxide (...
PUM
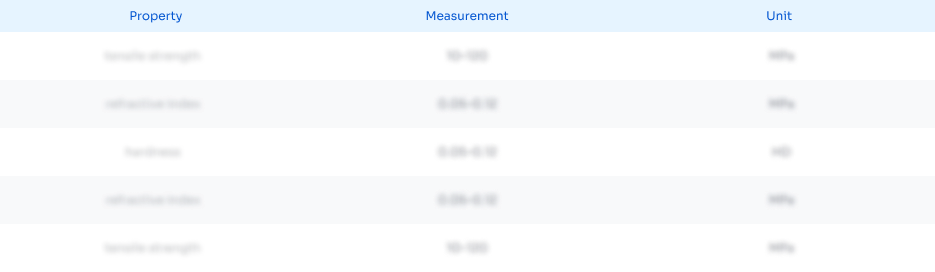
Abstract
Description
Claims
Application Information

- R&D Engineer
- R&D Manager
- IP Professional
- Industry Leading Data Capabilities
- Powerful AI technology
- Patent DNA Extraction
Browse by: Latest US Patents, China's latest patents, Technical Efficacy Thesaurus, Application Domain, Technology Topic, Popular Technical Reports.
© 2024 PatSnap. All rights reserved.Legal|Privacy policy|Modern Slavery Act Transparency Statement|Sitemap|About US| Contact US: help@patsnap.com