Pressure-equalizing and bleeding method for injecting furnace roof tank coal gas by using high-pressure gas
A high-pressure gas, material tank technology, applied in blast furnaces, blast furnace details, blast furnace parts and other directions, can solve problems such as environmental pollution, avoid environmental pollution and resource waste, good economic and social benefits, and consistent operating procedures.
- Summary
- Abstract
- Description
- Claims
- Application Information
AI Technical Summary
Problems solved by technology
Method used
Image
Examples
Embodiment 1
[0036] When equalizing the pressure on the top of the blast furnace, the traditional pressure equalizing method is adopted, that is, the pressure equalizing valve 8 and the equalizing pressure relief valve 5 are opened once, and the semi-clean gas that has been dedusted by the gravity dust collector enters the weighing material tank 3 through the equalizing pressure relief pipe 4, And the dust in the cyclone dust collector 7 is blown back into the weighing tank 3 . If the primary pressure equalization cannot meet the requirements, open the secondary pressure charging valve 9 again, and carry out secondary pressure equalization on the weighing tank 3 with nitrogen to meet the appropriate pressure requirement; after the equalization is completed, close the relevant valves and open the feeding gate 2 , the charge enters the blast furnace from the weighing tank 3 through the blanking gate 2.
[0037] When venting from the top of the blast furnace, open the pressure equalizing vent...
Embodiment 2
[0039] During pressure equalization, the traditional pressure equalization method is adopted, that is, the pressure equalization valve 8 and the pressure equalization release valve 5 are opened once, and the semi-clean gas that has been dedusted by the gravity dust collector enters the weighing material tank 3 through the pressure equalization release pipe 4, and the cyclone The dust in the dust collector 7 is blown back into the weighing tank 3 . If the primary pressure equalization cannot meet the requirements, open the secondary pressure charging valve 9 again, and carry out secondary pressure equalization on the weighing tank 3 with nitrogen to meet the appropriate pressure requirement; after equalizing the pressure, close the relevant valves and open the feeding gate 2 , the charge enters the blast furnace from the weighing tank 3 through the blanking gate 2.
[0040]When releasing, open the pressure equalizing release valve 5, the bag filter valve 11 and the natural reco...
Embodiment 3
[0042] During pressure equalization, the traditional pressure equalization method is adopted, that is, the pressure equalization valve 8 and the pressure equalization release valve 5 are opened once, and the semi-clean gas that has been dedusted by the gravity dust collector enters the weighing material tank 3 through the pressure equalization release pipe 4, and the cyclone The dust in the dust collector 7 is blown back into the weighing tank 3 . If the primary pressure equalization cannot meet the requirements, open the secondary pressure charging valve 9 again, and carry out secondary pressure equalization on the weighing tank 3 with nitrogen to meet the appropriate pressure requirement; after the equalization is completed, close the relevant valves and open the feeding gate 2 , the charge enters the blast furnace from the weighing tank 3 through the blanking gate 2.
[0043] When releasing, open the pressure equalizing release valve 5, the bag filter valve 11 and the natur...
PUM
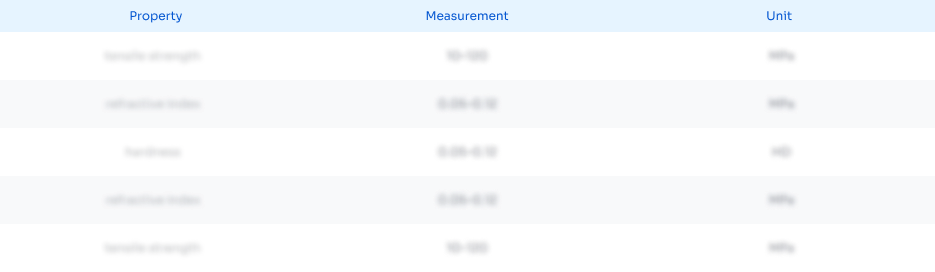
Abstract
Description
Claims
Application Information

- R&D
- Intellectual Property
- Life Sciences
- Materials
- Tech Scout
- Unparalleled Data Quality
- Higher Quality Content
- 60% Fewer Hallucinations
Browse by: Latest US Patents, China's latest patents, Technical Efficacy Thesaurus, Application Domain, Technology Topic, Popular Technical Reports.
© 2025 PatSnap. All rights reserved.Legal|Privacy policy|Modern Slavery Act Transparency Statement|Sitemap|About US| Contact US: help@patsnap.com