Polyester molding plastic and preparation method thereof
A molding compound and polyester technology, applied in the field of polyester molding compound and its preparation, can solve the problems of surface yellowing, affecting the use effect of parts, and unsatisfactory use, and achieve the effect of reducing the content
- Summary
- Abstract
- Description
- Claims
- Application Information
AI Technical Summary
Problems solved by technology
Method used
Image
Examples
Embodiment 1
[0022] Weigh according to the formula measurement components: 70 parts of unsaturated polyester resin, 30 parts of Palapreg H 870-901, 200 parts of aluminum hydroxide powder, 6 parts of HD-S, 1 part of Luperox TBICM75, 1 part of calcium hydroxide powder, BYK- 6 parts of P9080, 60 parts of 6mm glass fiber, the above parts are parts by weight.
[0023] According to the above formula, first pour the unsaturated polyester resin, low shrinkage additives, initiator, internal release agent into the kneader and mix for 2 minutes; then add inorganic mineral fillers, white pigments and calcium hydroxide powder and mix for 40 minutes; Finally, glass fiber is added, and the polyester molding compound of the present invention can be obtained after mixing for 10 minutes.
[0024] Table 1 below shows the effect of different low-shrinkage additives on yellowing after 7 days at 160 degrees Celsius under the condition that the dosages of other components remain unchanged:
[0025] Table 1
[0026]
[...
Embodiment 2
[0029] Weigh according to the components of the formula: 60 parts of unsaturated polyester resin, 40 parts of Palapreg H 851-02, 250 parts of calcium carbonate powder, 2 parts of HD-S, 2 parts of Luperox 256, 0.6 parts of calcium hydroxide powder, BYK-P90652 Parts, 50 parts of 3mm glass fiber, the above parts are parts by weight.
[0030] According to the above formula, first pour the unsaturated polyester resin, low shrinkage additives, initiator, internal release agent into the kneader and mix for 5 minutes; then add inorganic mineral fillers, white pigments and calcium hydroxide powder and mix for 30 minutes; Finally, add glass fiber and mix for 7 minutes to obtain the polyester molding compound of the present invention
[0031] With the other components unchanged, test the effect of different initiator types on yellowing after 7 days at 160 degrees Celsius:
[0032] The results are shown in Table 2:
[0033] Table 2
[0034]
[0035] It can be seen from the data shown in the above...
Embodiment 3
[0037] Weigh according to the components of the formula: 65 parts of unsaturated polyester resin, 120 parts of Palapreg H 2073 35 parts of calcium carbonate powder, 100 parts of aluminum hydroxide powder, 4 parts of HD-S, 1.5 parts of Luperox TBEC, and 0.8 parts of calcium hydroxide powder. Parts, BYK-P9050 4 parts, 12mm glass fiber 35 parts, 3mm glass fiber 10 parts, the above parts are parts by weight.
[0038] According to the above formula, first pour the unsaturated polyester resin, low shrinkage additives, initiator, internal release agent into the kneader and mix for 3 minutes; then add inorganic mineral fillers, white pigments and calcium hydroxide powder and mix for 35 minutes; Finally, add glass fiber and mix for 5 minutes to obtain the polyester molding compound of the present invention
[0039] The dosage of other components remains unchanged, and the effect of different internal mold release agents on yellowing is tested after 7 days at 160 degrees Celsius:
[0040] The...
PUM
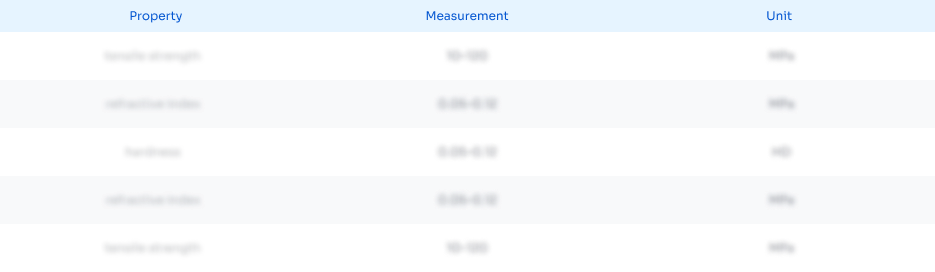
Abstract
Description
Claims
Application Information

- Generate Ideas
- Intellectual Property
- Life Sciences
- Materials
- Tech Scout
- Unparalleled Data Quality
- Higher Quality Content
- 60% Fewer Hallucinations
Browse by: Latest US Patents, China's latest patents, Technical Efficacy Thesaurus, Application Domain, Technology Topic, Popular Technical Reports.
© 2025 PatSnap. All rights reserved.Legal|Privacy policy|Modern Slavery Act Transparency Statement|Sitemap|About US| Contact US: help@patsnap.com