Polyester molding compound and preparation method thereof
A molding compound and polyester technology, which is applied in the field of polyester molding compound and its preparation, can solve the problems of surface yellowing, unsatisfactory use, and affecting the use effect of parts, and achieve the effect of reducing the content
- Summary
- Abstract
- Description
- Claims
- Application Information
AI Technical Summary
Problems solved by technology
Method used
Image
Examples
Embodiment 1
[0022] Weigh the components according to the formula: 70 parts of unsaturated polyester resin, 30 parts of Palapreg H 870-901, 200 parts of aluminum hydroxide powder, 6 parts of HD-S, 1 part of Luperox TBICM75, 1 part of calcium hydroxide powder, BYK- 6 parts of P9080, 60 parts of 6mm glass fiber, the above-mentioned parts are parts by weight.
[0023] According to the above formula, pour the unsaturated polyester resin, low shrinkage additive, initiator, and internal release agent into the kneader and knead for 2 minutes; then add inorganic mineral fillers, white pigments and calcium hydroxide micropowder and knead for 40 minutes; Finally, glass fiber is added, and the polyester molding compound of the present invention can be obtained after kneading for 10 minutes.
[0024] The following table 1 shows the effect of different low shrinkage additives on yellowing after 7 days of testing at 160 degrees Celsius under the condition that the dosage of other components remains unch...
Embodiment 2
[0029] Weigh the components according to the formula: 60 parts of unsaturated polyester resin, 40 parts of Palapreg H 851-02, 250 parts of calcium carbonate micropowder, 2 parts of HD-S, 2 parts of Luperox 256, 0.6 part of calcium hydroxide micropowder, BYK-P90652 Parts, 50 parts of 3mm glass fibers, the above-mentioned parts are parts by weight.
[0030] According to the above formula, first pour the unsaturated polyester resin, low shrinkage additive, initiator, and internal release agent into the kneader and knead for 5 minutes; then add inorganic mineral fillers, white pigments and calcium hydroxide micropowder and knead for 30 minutes; Add glass fiber at last, after mixing for 7 minutes, the polyester molding compound of the present invention can be obtained
[0031] Under the condition that other components are constant, test the influence of different initiator types on yellowing after 7 days at 160 degrees Celsius:
[0032] The results are shown in Table 2:
[0033] ...
Embodiment 3
[0037] Weigh the components according to the formula: 65 parts of unsaturated polyester resin, 35 parts of Palapreg H 2073 calcium carbonate micropowder 120 parts, aluminum hydroxide micropowder 100 parts, HD-S 4 parts, Luperox TBEC 1.5 parts, calcium hydroxide micropowder 0.8 Parts, 4 parts of BYK-P9050, 35 parts of 12mm glass fiber, 10 parts of 3mm glass fiber, the above-mentioned parts are parts by weight.
[0038] According to the above formula, first pour the unsaturated polyester resin, low shrinkage additive, initiator, and internal mold release agent into the kneader and knead for 3 minutes; then add inorganic mineral fillers, white pigments and calcium hydroxide micropowder and knead for 35 minutes; Add glass fiber at last, after kneading for 5 minutes, the polyester molding compound of the present invention can be obtained
[0039] The dosage of other components remains unchanged, and the influence of different internal mold release agents on yellowing after 7 days a...
PUM
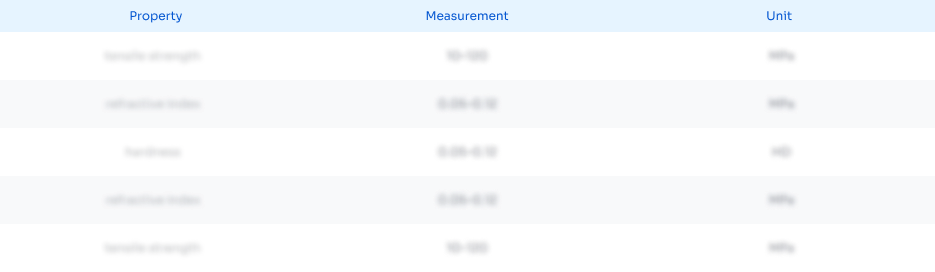
Abstract
Description
Claims
Application Information

- R&D Engineer
- R&D Manager
- IP Professional
- Industry Leading Data Capabilities
- Powerful AI technology
- Patent DNA Extraction
Browse by: Latest US Patents, China's latest patents, Technical Efficacy Thesaurus, Application Domain, Technology Topic, Popular Technical Reports.
© 2024 PatSnap. All rights reserved.Legal|Privacy policy|Modern Slavery Act Transparency Statement|Sitemap|About US| Contact US: help@patsnap.com