MEMS (micro-electromechanical systems) device and vacuum encapsulation method of wafer level thereof
A device and silicon structure technology, which is applied in the field of MEMS devices and their vacuum packaging based on silicon-silicon bonding technology, can solve the problems of poor air tightness and difficult electrical interconnection of MEMS devices in wafer-level vacuum packaging, and is convenient for promotion and application. , Reduce the cost of packaging, good air tightness
- Summary
- Abstract
- Description
- Claims
- Application Information
AI Technical Summary
Problems solved by technology
Method used
Image
Examples
Embodiment Construction
[0021] The present invention will be further described below in conjunction with the accompanying drawings.
[0022] 1. MEMS device structure:
[0023] Such as figure 1 , figure 2 As shown, the MEMS device is composed of a silicon substrate layer 10 , a silicon structure layer 15 and a silicon capping layer 12 .
[0024] The surface of the silicon substrate 10 is etched to form a shallow cavity 8, so that a certain distance is formed between the movable structure 6 and the substrate, so as to avoid hindering the movement of the movable structure. The silicon capping layer 12 etches the shallow cavity 9 and the lead through hole 13 , and the position and shape of the shallow cavity 9 correspond to that of the shallow cavity 8 on the silicon substrate. The surfaces of the silicon substrate 10 and the silicon cap 12 respectively have a certain thickness of an oxide layer 7 and an oxide layer 11 , which are bonded to the silicon structure layer 15 to play an insulating role. ...
PUM
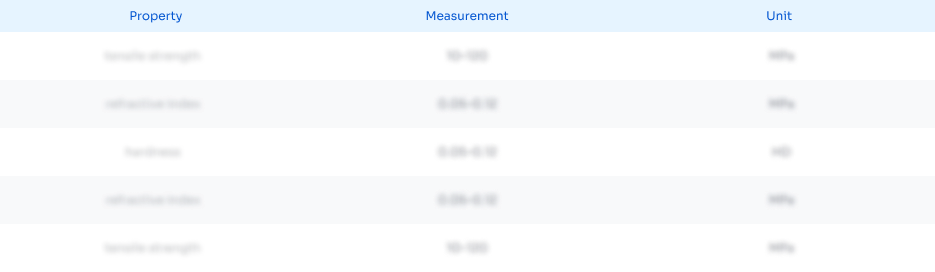
Abstract
Description
Claims
Application Information

- Generate Ideas
- Intellectual Property
- Life Sciences
- Materials
- Tech Scout
- Unparalleled Data Quality
- Higher Quality Content
- 60% Fewer Hallucinations
Browse by: Latest US Patents, China's latest patents, Technical Efficacy Thesaurus, Application Domain, Technology Topic, Popular Technical Reports.
© 2025 PatSnap. All rights reserved.Legal|Privacy policy|Modern Slavery Act Transparency Statement|Sitemap|About US| Contact US: help@patsnap.com