Film material for greenhouse and preparation method of film material
A technology of film materials and greenhouses, which is applied in the field of film materials for greenhouses and its preparation, can solve the problems affecting the growth of plants or vegetables in greenhouses, deformation and water evaporation, and low physical properties, achieving high tear strength, Prevents water loss, improves performance and quality
- Summary
- Abstract
- Description
- Claims
- Application Information
AI Technical Summary
Problems solved by technology
Method used
Image
Examples
Embodiment 1
[0044] (1) Start the high-speed mixer, and add 62 parts of PE, 30 parts of PVC, 10 parts of polyethylene glycol diacrylate, 2 parts of methyltriacetoxysilane, trimethyl 6 parts of siloxysilicate, 9 parts of poly-1,4-butylene adipate, 1 part of polyglycerol ricinoleate, 2 parts of triethyl citrate, add the above materials and mix at high speed until uniform; (2) Extrude the uniformly mixed material with a twin-screw extruder and perform extrusion granulation. The extrusion temperatures of the twin-screw extruder are: the temperature of the first stage is 169 ° C, and the temperature of the second stage is 174°C, the temperature of the third stage is 193°C, the temperature of the fourth stage is 202°C, the length-to-diameter ratio of the twin-screw extruder is 30:1, and the mixture is cut into pellets after twin-screw extrusion; (3) blown film The machine plasticizes the material in step (2) and then extrudes it. When extruding after plasticization, the feeding temperature is 12...
Embodiment 2
[0046] (1) Start the high-speed mixer, and add 36 parts of PE, 55 parts of PVC, 4 parts of polyethylene glycol diacrylate, 6 parts of methyltriacetoxysilane, trimethyl 2 parts of siloxysilicate, 3 parts of poly-1,4-butylene adipate, 4 parts of polyglycerol ricinoleate, 0.5 part of triethyl citrate, add the above materials and mix at high speed (2) Use twin-screw extruder to extrude and granulate the mixed material after mixing evenly. 182°C, the temperature of the third stage is 188°C, the temperature of the fourth stage is 195°C, the length-to-diameter ratio of the twin-screw extruder is 20:1, and the mixture is cut into pellets after twin-screw extrusion; (3) blown film The machine plasticizes the material in step (2) and then extrudes it. When extruding after plasticization, the feeding temperature is 120°C, the compression plasticizing temperature is 155°C, and the head temperature is 165°C; (4) the step (3) The material is towed, the inflation ratio is 1:3, and the tract...
Embodiment 3
[0048](1) Start the high-speed mixer, and add 56 parts of PE, 50 parts of PVC, 5 parts of polyethylene glycol diacrylate, 5 parts of methyltriacetoxysilane, trimethyl 3 parts of siloxysilicate, 4 parts of poly-1,4-butylene adipate, 3 parts of polyglycerol ricinoleate, 1.6 parts of triethyl citrate, add the above materials and mix at high speed until uniform; (2) Extrude the uniformly mixed material with a twin-screw extruder and perform extrusion granulation. The extrusion temperatures of the twin-screw extruder are: the temperature of the first stage is 169 ° C, and the temperature of the second stage is 174°C, the temperature of the third stage is 193°C, the temperature of the fourth stage is 202°C, the length-to-diameter ratio of the twin-screw extruder is 30:1, and the mixture is cut into pellets after twin-screw extrusion; (3) blown film The machine plasticizes the material in step (2) and then extrudes it. When extruding after plasticization, the feeding temperature is 1...
PUM
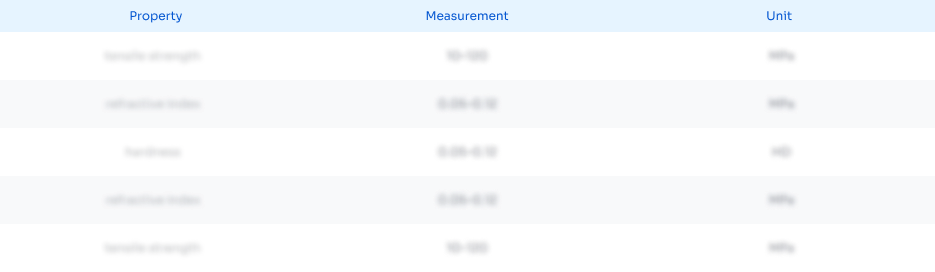
Abstract
Description
Claims
Application Information

- R&D
- Intellectual Property
- Life Sciences
- Materials
- Tech Scout
- Unparalleled Data Quality
- Higher Quality Content
- 60% Fewer Hallucinations
Browse by: Latest US Patents, China's latest patents, Technical Efficacy Thesaurus, Application Domain, Technology Topic, Popular Technical Reports.
© 2025 PatSnap. All rights reserved.Legal|Privacy policy|Modern Slavery Act Transparency Statement|Sitemap|About US| Contact US: help@patsnap.com