Copper-nickel 34 metal wire and preparation method thereof
- Summary
- Abstract
- Description
- Claims
- Application Information
AI Technical Summary
Problems solved by technology
Method used
Image
Examples
Embodiment 1
[0044] The copper-nickel 34 metal wire in this embodiment is composed of 33% Ni, 0.6% Mn, 0.01% Fe, 0.01% Ti, 0.01% B, 0.05% Re and 66.32% copper.
[0045] Copper Nickel 34 wire was prepared by:
[0046] (1) Mix and melt the raw materials, peel and forge the obtained ingot;
[0047] (2) After drawing the forged billet to obtain a filament with a diameter of 4.0mm, draw it again to obtain a filament with a diameter of 1.0mm, then anneal it, draw it again to obtain a filament with a diameter of 0.3mm, anneal it, and then draw it again The filaments with a diameter of 0.15 mm are pulled out and then annealed to finally obtain filaments with a diameter of 0.15 mm.
Embodiment 2
[0049] Copper Nickel 34 wire consists of 35% Ni, 0.05% Mn, 0.5% Fe, 0.3% Ti, 0.1% B, 0.001% Re, 0.3% Si, and 63.749% Copper.
[0050] Copper Nickel 34 wire was prepared by:
[0051] (1) Mix and melt the raw materials, peel and forge the obtained ingot;
[0052] (2) After drawing the forged billet to obtain a filament with a diameter of 8.0mm, draw it again to obtain a filament with a diameter of 6.0mm, then anneal, repeat drawing and annealing 6 times, and finally obtain a filament with a diameter of 0.05mm .
Embodiment 3
[0054] Copper Nickel 34 wire consists of 34% Ni, 0.3% Mn, 0.1% Fe, 0.15% Ti, 0.05% V, 0.04% B, 0.03% Re, and 65.33% Copper.
[0055] Copper Nickel 34 wire was prepared by:
[0056] (1) Mix and melt the raw materials, peel and forge the obtained ingot;
[0057] (2) After drawing the forged billet to obtain a filament with a diameter of 6.0mm, draw it again to obtain a filament with a diameter of 4.0mm, then anneal, repeat the drawing and annealing 3 times, and finally obtain a filament with a diameter of 0.1mm .
PUM
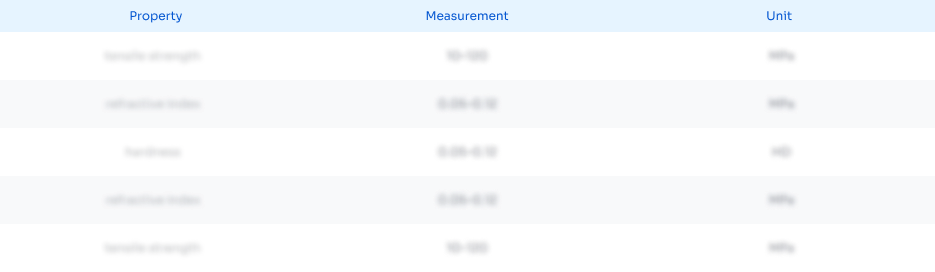
Abstract
Description
Claims
Application Information

- R&D
- Intellectual Property
- Life Sciences
- Materials
- Tech Scout
- Unparalleled Data Quality
- Higher Quality Content
- 60% Fewer Hallucinations
Browse by: Latest US Patents, China's latest patents, Technical Efficacy Thesaurus, Application Domain, Technology Topic, Popular Technical Reports.
© 2025 PatSnap. All rights reserved.Legal|Privacy policy|Modern Slavery Act Transparency Statement|Sitemap|About US| Contact US: help@patsnap.com