Preparation method of polymeric phosphorus-nitrogen flame retardant
A phosphorus-nitrogen flame retardant, a polymerized technology, is applied in the field of the preparation of polymerized phosphorus-nitrogen flame retardants, and can solve the problem of mechanical properties such as elongation at break, tensile strength, etc. The effect is not obvious and other problems, to achieve the effect of simple post-processing process, simple production conditions, high product purity and yield
- Summary
- Abstract
- Description
- Claims
- Application Information
AI Technical Summary
Problems solved by technology
Method used
Examples
Embodiment 1
[0018] Add phenylphosphorous dichloride (8.950g, 0.05mol) and 50ml ethyl acetate to a 250ml four-neck flask equipped with a thermometer, nitrogen gas introduction, 100ml constant pressure dropping funnel, magneton, reflux condenser and tail gas absorption device , Dissolving m-xylylenediamine (6.870g, 0.05mol) in 50ml ethyl acetate was added to a constant pressure funnel. Under nitrogen protection and stirring, m-xylylenediamine solution was slowly added dropwise. After the dropwise addition, the temperature was raised to the reflux temperature to continue the reaction for 5 hours, and after the reaction was completed, the nitrogen was continued. 2 Bring to room temperature. Then the mixture was suction-filtered under reduced pressure, and the filter cake was washed with 100 ml of ethyl acetate, and vacuum-dried at 100° C. for 6 hours to obtain 10.63 g of a white solid, with a yield of 87.3%.
Embodiment 2
[0020] Add phenylphosphorous dichloride (8.950g, 0.05mol) and 50ml chloroform to a 250ml four-necked flask equipped with a thermometer, nitrogen gas introduction, 100ml constant pressure dropping funnel, magneton, reflux condenser and tail gas absorption device. m-Xylylenediamine (6.870g, 0.05mol) was dissolved in 50ml of chloroform and added to the constant pressure funnel. Under nitrogen protection and stirring, m-xylylenediamine solution was slowly added dropwise. After the dropwise addition, the temperature was raised to the reflux temperature to continue the reaction for 6 hours, and after the reaction was completed, the nitrogen was continued. 2 Bring to room temperature. Then the mixture was suction-filtered under reduced pressure, and the filter cake was washed with 100 ml of chloroform, and vacuum-dried at 100° C. for 6 hours to obtain 9.31 g of a white solid, with a yield of 76.5%.
Embodiment 3
[0022] Add phenyl phosphorus dichloride (26.85g, 0.15mol) and 100ml dichloromethane to a 250ml four-neck flask equipped with a thermometer, nitrogen gas introduction, 100ml constant pressure dropping funnel, magneton, reflux condenser and tail gas absorption device , m-xylylenediamine (20.61g, 0.15mol) was dissolved in 100ml of dichloromethane, and added to a constant pressure funnel. Under nitrogen protection and stirring, m-xylylenediamine solution was slowly added dropwise. After the dropwise addition was completed, the temperature was raised to reflux temperature and the reaction was continued for 7 hours, and the N was continued after the reaction was completed. 2 Bring to room temperature. Then the mixture was suction-filtered under reduced pressure, and the filter cake was washed with 200ml of dichloromethane, and vacuum-dried at 100°C for 6 hours to obtain 28.53g of white solid, with a yield of 78.1%.
PUM
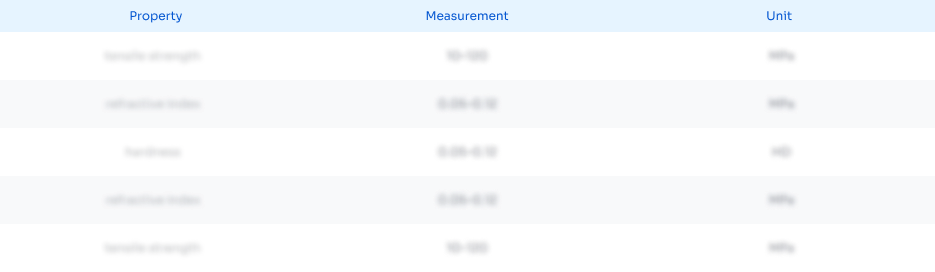
Abstract
Description
Claims
Application Information

- Generate Ideas
- Intellectual Property
- Life Sciences
- Materials
- Tech Scout
- Unparalleled Data Quality
- Higher Quality Content
- 60% Fewer Hallucinations
Browse by: Latest US Patents, China's latest patents, Technical Efficacy Thesaurus, Application Domain, Technology Topic, Popular Technical Reports.
© 2025 PatSnap. All rights reserved.Legal|Privacy policy|Modern Slavery Act Transparency Statement|Sitemap|About US| Contact US: help@patsnap.com