Method for preparing hydrogen by utilizing metallurgical slag waste heat to reform regenerative resources rich in methane
A technology for renewable resources and metallurgical slag, applied in chemical instruments and methods, hydrogen, non-metallic elements, etc., can solve the problems of low recovery efficiency of slag waste heat and high cost of hydrogen production process
- Summary
- Abstract
- Description
- Claims
- Application Information
AI Technical Summary
Problems solved by technology
Method used
Image
Examples
Embodiment 1
[0029] The mixed gas of carbon dioxide, methane and water vapor is passed into the heat exchange bed with blast furnace slag according to the volume fraction of 74% carbon dioxide, 13% methane and 13% water vapor, and the gas flow rate is 1.5m / s~4m / s s, the flow velocity of blast furnace slag is 0.01m / s. The gas is fully preheated in the fluidized bed, the temperature of the slag is lowered, and the solidification process and granulation are carried out at the same time. By controlling the air velocity, the obtained slag particles are brought into the slag chamber in the air flow bed to form a high-temperature slag layer. The gas is further heated through the high-temperature slag layer, and then undergoes catalytic reforming hydrogen production reaction through the catalyst layer to generate carbon monoxide and hydrogen; the gas is converted into hydrogen through a CO device, and the hydrogen content is increased. In the ball milling system, the excess carbon dioxide gas in t...
Embodiment 2
[0031] The mixed gas of carbon dioxide, methane and water vapor is passed into the heat exchange bed with the converter slag according to the volume fraction of 70% carbon dioxide, 22% methane and 8% water vapor, and the gas flow rate is 1.5m / s~5m / s s, the flow velocity of converter slag is 0.01m / s. The gas is fully preheated in the fluidized bed, the temperature of the slag is lowered, and the solidification process and granulation are carried out at the same time. By controlling the air velocity, the obtained slag particles are brought into the slag chamber in the air flow bed to form a high-temperature slag layer. The gas is further heated through the high-temperature slag layer, and then undergoes catalytic reforming hydrogen production reaction through the catalyst layer to generate carbon monoxide and hydrogen; the gas is converted into hydrogen through a CO device, and the hydrogen content is increased. In the ball milling system, the excess carbon dioxide gas in the sy...
Embodiment 3
[0033] The mixed gas of carbon dioxide, methane and water vapor is passed into the heat exchange bed with ferronickel slag according to the volume fraction of 62% carbon dioxide, 18% methane and 20% water vapor, and the gas flow rate is 1.5m / s~5m / s, the flow velocity of ferronickel slag is 0.01m / s. The gas is fully preheated in the fluidized bed, the temperature of the slag is lowered, and the solidification process and granulation are carried out at the same time. By controlling the air velocity, the obtained slag particles are brought into the slag chamber in the air flow bed to form a high-temperature slag layer. The gas is further heated through the high-temperature slag layer, and then undergoes catalytic reforming hydrogen production reaction through the catalyst layer to generate carbon monoxide and hydrogen; the gas is converted into hydrogen through a CO device, and the hydrogen content is increased. In the ball milling system, the excess carbon dioxide gas in the sy...
PUM
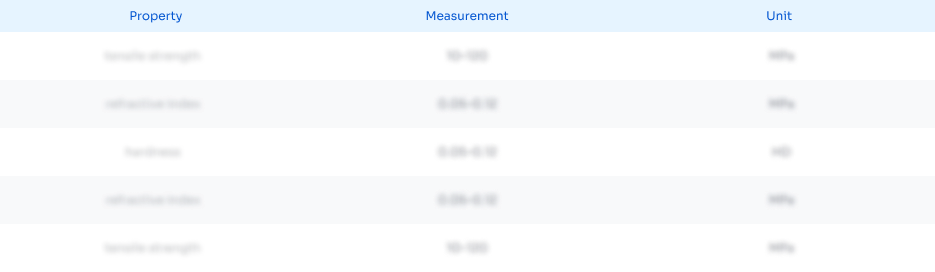
Abstract
Description
Claims
Application Information

- R&D
- Intellectual Property
- Life Sciences
- Materials
- Tech Scout
- Unparalleled Data Quality
- Higher Quality Content
- 60% Fewer Hallucinations
Browse by: Latest US Patents, China's latest patents, Technical Efficacy Thesaurus, Application Domain, Technology Topic, Popular Technical Reports.
© 2025 PatSnap. All rights reserved.Legal|Privacy policy|Modern Slavery Act Transparency Statement|Sitemap|About US| Contact US: help@patsnap.com