3T1R four-degrees-of-freedom precise location workbench
A precision positioning and degree of freedom technology, applied in the field of micro-operating systems, can solve the problems of limited application range, high motion positioning accuracy, and unreachable problems, and achieve micro-feed and precise positioning, eliminate nonlinearity, and compact structure.
- Summary
- Abstract
- Description
- Claims
- Application Information
AI Technical Summary
Problems solved by technology
Method used
Image
Examples
Embodiment Construction
[0015] In order to further understand the invention content, characteristics and effects of the present invention, the following examples are given, and detailed descriptions are as follows in conjunction with the accompanying drawings:
[0016] see Figure 1 to Figure 6 , a 3T1R four-degree-of-freedom precision positioning workbench, including a moving platform 1, a flexible end support frame 2, four flexible branch chains 3-1, 3-2, 3-3, 3-4, a base 4 and four pressing Electroceramic driver.
[0017] The flexible end support frame 2 is in the shape of "I", located between the top ends of the four flexible branch chains 3-1, 3-2, 3-3, 3-4 and the moving platform 1, including a rigid support 21 with a circular cross section and two rigid connectors 25, the vertical ends of the rigid support 21 are respectively connected to the two rigid connectors 25 through the first elastic hinges 22, 23, and the left and right ends of the two rigid connectors 25 are respectively provided wi...
PUM
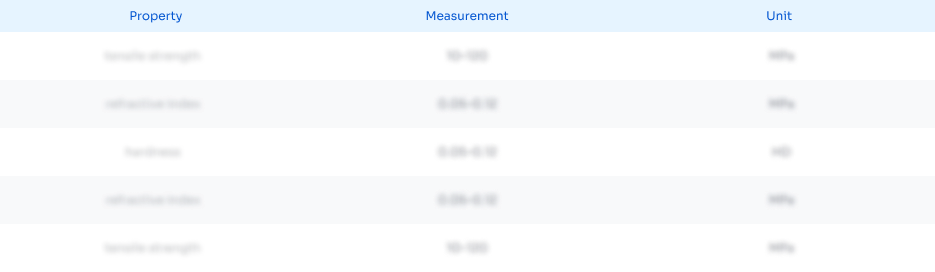
Abstract
Description
Claims
Application Information

- R&D Engineer
- R&D Manager
- IP Professional
- Industry Leading Data Capabilities
- Powerful AI technology
- Patent DNA Extraction
Browse by: Latest US Patents, China's latest patents, Technical Efficacy Thesaurus, Application Domain, Technology Topic, Popular Technical Reports.
© 2024 PatSnap. All rights reserved.Legal|Privacy policy|Modern Slavery Act Transparency Statement|Sitemap|About US| Contact US: help@patsnap.com