A three-degree-of-freedom piezoelectric-driven micro-nano positioning platform
A piezoelectric drive and micro-nano positioning technology, which is applied in the direction of machines/supports, supporting machines, mechanical equipment, etc., can solve the problem that the output displacement of the platform cannot meet the requirements of sufficient work space, multi-degree-of-freedom work requirements, and positioning accuracy Can not meet the requirements and other problems, to achieve the effect of good output motion stability, three-dimensional scanning motion, high natural frequency and reliability
- Summary
- Abstract
- Description
- Claims
- Application Information
AI Technical Summary
Problems solved by technology
Method used
Image
Examples
Embodiment Construction
[0047] Below in conjunction with embodiment and accompanying drawing thereof, technical scheme of the present invention is described in further detail:
[0048] A three-degree-of-freedom piezoelectric-driven micro-nano positioning platform, its structure is as follows Figure 1-5 Shown:
[0049]Including a two-degree-of-freedom parallel motion platform and a single-degree-of-freedom motion platform in series, three stacked piezoelectric ceramic drivers are required.
[0050] The two-degree-of-freedom parallel motion platform includes a lower base 1, an XY-direction motion platform 4, two composite bridge-type displacement amplification mechanisms 6, four sets of semicircular hinge branch chain decoupling mechanisms 3, and four sets of guide mechanisms 5.
[0051] In the lower base 1, two adjacent side walls are respectively connected to a composite bridge-type displacement amplifying mechanism 6, and the other two adjacent side walls of the lower base 1 are connected to two s...
PUM
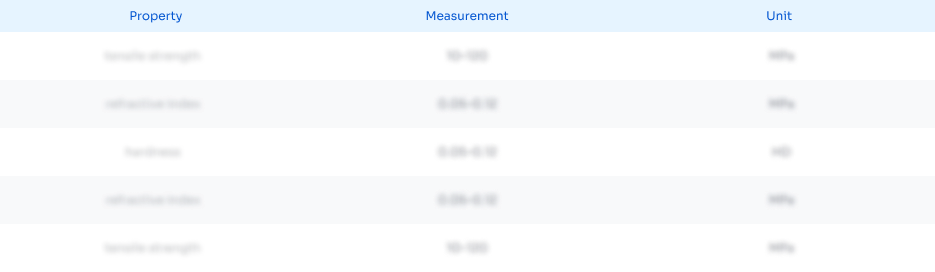
Abstract
Description
Claims
Application Information

- Generate Ideas
- Intellectual Property
- Life Sciences
- Materials
- Tech Scout
- Unparalleled Data Quality
- Higher Quality Content
- 60% Fewer Hallucinations
Browse by: Latest US Patents, China's latest patents, Technical Efficacy Thesaurus, Application Domain, Technology Topic, Popular Technical Reports.
© 2025 PatSnap. All rights reserved.Legal|Privacy policy|Modern Slavery Act Transparency Statement|Sitemap|About US| Contact US: help@patsnap.com