Residual oil hydrotreating process
A technology for hydrogenation and treatment of residue oil, which is applied in the fields of hydrotreating process, petroleum industry, treatment of hydrocarbon oil, etc., can solve the problems of large coke generation, reducing the treatment capacity of the device and economic benefits, and increasing the load of the regenerator.
- Summary
- Abstract
- Description
- Claims
- Application Information
AI Technical Summary
Problems solved by technology
Method used
Image
Examples
Embodiment 1
[0037] The residual oil and hydrogen mixed oil directly enter the residual oil hydrogenation pilot plant, and the catalytic cracking back to the refinery uses the filtered catalytic cracking heavy cycle oil, which enters the residual oil hydrogenation reactor through the front feed port of the demetallization agent bed, and also according to the table The reaction is carried out under the conditions in 3, and the reaction products are separated into gas, hydrogenated naphtha, hydrogenated diesel oil, and hydrogenated residue; the hydrogenated residue enters the catalytic cracking unit to continue the reaction, and the products are separated into dry gas, catalytic gasoline, catalytic Diesel, heavy cycle oil, oil slurry. See Table 3 for product properties and operating conditions.
Embodiment 2
[0044] The residual oil and hydrogen mixed oil directly enter the residual oil hydrogenation pilot plant, and the catalytic cracking oil refining uses catalytic cracking oil slurry. After filtering, it enters the residual oil hydrogenation reactor through the front feed port of the demetallization agent bed, and also according to the table The reaction is carried out under the conditions in 1, and the reaction products are separated into gas, hydrogenated naphtha, hydrogenated diesel oil, and hydrogenated residue; the hydrogenated residue enters the catalytic cracking unit to continue the reaction, and the products are separated into dry gas, catalytic gasoline, catalytic Diesel, heavy cycle oil, oil slurry. The properties and operation of the product are shown in Table 4.
Embodiment 3
[0051] The residual oil and hydrogen mixed oil directly enter the residual oil hydrogenation pilot plant, and the catalytic cracking and refining oil adopts catalytic cracking heavy cycle oil: catalytic cracking oil slurry: 5:5, after filtering, it enters through the front feed port of the demetallizer bed The residual oil hydrogenation reactor also reacts according to the conditions in Table 1, and the reaction products are separated into gas, hydrogenated naphtha, hydrogenated diesel oil, and hydrogenated residual oil; the hydrogenated residual oil enters the catalytic cracking unit to continue the reaction, The products are separated into dry gas, catalytic gasoline, catalytic diesel, heavy cycle oil and oil slurry. The properties and operation of the product are shown in Table 5.
PUM
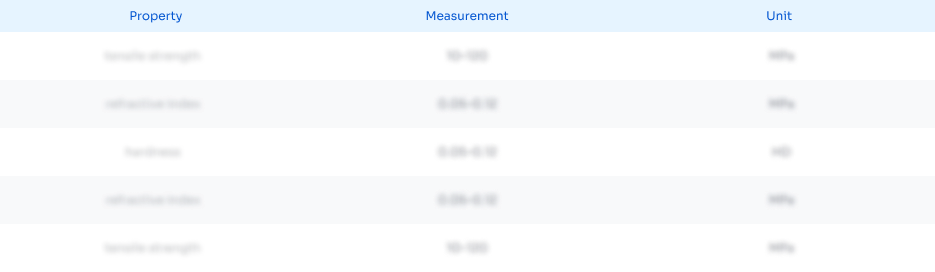
Abstract
Description
Claims
Application Information

- R&D Engineer
- R&D Manager
- IP Professional
- Industry Leading Data Capabilities
- Powerful AI technology
- Patent DNA Extraction
Browse by: Latest US Patents, China's latest patents, Technical Efficacy Thesaurus, Application Domain, Technology Topic, Popular Technical Reports.
© 2024 PatSnap. All rights reserved.Legal|Privacy policy|Modern Slavery Act Transparency Statement|Sitemap|About US| Contact US: help@patsnap.com