Preparation method for vertical type continuous graphitizing furnace carbon black brick
A technology of graphitization furnace and carbon black, which is applied in the field of preparation of carbon black bricks of vertical continuous graphitization furnace, which can solve the problems of unfavorable total power of graphitization furnace, smaller furnace resistance, and smaller distance, so as to facilitate production and operation Parameter adjustment, avoiding dead furnace phenomenon, and the effect of total power improvement
- Summary
- Abstract
- Description
- Claims
- Application Information
AI Technical Summary
Problems solved by technology
Method used
Examples
Embodiment 1
[0014] A method for preparing carbon black bricks in a vertical continuous graphitization furnace. The preparation steps are as follows: carbon black and pitch are mixed in a ratio of 1.7:1, and then heated and kneaded in a kneader at a temperature of 180°C. The press is pressed (pressed into a certain shape) with a pressure of 1000KN, and then roasted in a roasting kiln at a roasting temperature of 800°C, and finally crushed. The particle size of the crushed mixture is 80 mesh, and the first stage can be obtained. Material; mix the first-stage material and asphalt in a ratio of 2.5:1, then heat and knead in a kneader at a temperature of 180°C, and then press the mold loaded with the mixture by a press at a pressure of 6000KN , and then roasted in a roasting kiln at a roasting temperature of 800°C, and finally kept at 800°C for 2 hours, and then left the kiln after it cooled naturally.
Embodiment 2
[0016] A method for preparing carbon black bricks in a vertical continuous graphitization furnace. The preparation steps are as follows: carbon black and pitch are mixed in a ratio of 2:1, and then heated and kneaded in a kneader at a temperature of 200°C. The press is pressed (pressed into a certain shape) with a pressure of 2000KN, and then roasted in a roasting kiln at a roasting temperature of 900°C, and finally crushed. The particle size of the crushed mixture is 100 mesh, and the first stage can be obtained. Material; mix the first-stage material and asphalt in a ratio of 3:1, then heat and knead in a kneader at a temperature of 200°C, and then press the mold loaded with the mixture by a press at a pressure of 8000KN , and then roasted in a roasting kiln at a roasting temperature of 1000 ° C, and finally kept at 1000 ° C for 5 hours, and then left the kiln after it cooled naturally.
Embodiment 3
[0018] A method for preparing carbon black bricks for a vertical continuous graphitization furnace. The preparation steps are as follows: carbon black and pitch are mixed in a ratio of 2.5:1, and then heated and kneaded in a kneader at a temperature of 250°C. The press is pressed (pressed into a certain shape) with a pressure of 3000KN, and then roasted in a roasting kiln at a roasting temperature of 950°C, and finally crushed. The particle size of the crushed mixture is 120 mesh, and the first stage can be obtained. Material; mix the first-stage material and asphalt in a ratio of 3.5:1, then heat and knead in a kneader at a temperature of 250°C, and then press the mold loaded with the mixture by a press at a pressure of 10,000KN , and then roasted in a roasting kiln at a roasting temperature of 1100 ° C, and finally kept at 1100 ° C for 8 hours, and then left the kiln after it cooled naturally.
[0019] Carbon black brick prepared by the method of the present invention and gr...
PUM
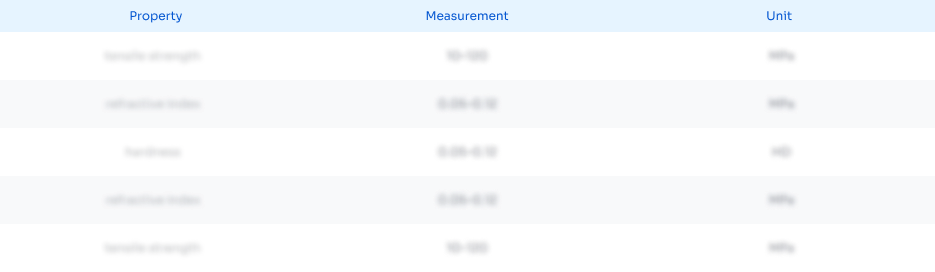
Abstract
Description
Claims
Application Information

- R&D
- Intellectual Property
- Life Sciences
- Materials
- Tech Scout
- Unparalleled Data Quality
- Higher Quality Content
- 60% Fewer Hallucinations
Browse by: Latest US Patents, China's latest patents, Technical Efficacy Thesaurus, Application Domain, Technology Topic, Popular Technical Reports.
© 2025 PatSnap. All rights reserved.Legal|Privacy policy|Modern Slavery Act Transparency Statement|Sitemap|About US| Contact US: help@patsnap.com