Method for preparing polyimide in supercritical carbon dioxide
A carbon dioxide and polyimide technology, applied in the production of bulk chemicals, etc., can solve problems such as high pollution, difficult solvent treatment, unstable quality of melt polymerization products, etc., and achieve the effect of pure products and simple and practical methods
- Summary
- Abstract
- Description
- Claims
- Application Information
AI Technical Summary
Problems solved by technology
Method used
Image
Examples
Embodiment 1
[0018] Add 200g 4,4'-diaminodiphenyl ether, 215g pyromellitic dianhydride, 4.14g phthalic anhydride and 22g pyridine in the autoclave under the protection of nitrogen, then close the reaction vessel, vacuumize and ventilate Add carbon dioxide, heat the temperature to 50°C, supplement the pressure of the reactor, when the temperature reaches 60°C, control the pressure of the reactor to 20MPa, turn on the electromagnetic stirring, after 3 hours of reaction, raise the temperature to 200°C, control the pressure of the reactor to 50MPa, continue React for 4 hours, end the reaction, slowly open the release valve, control the release time to 2 hours, to remove a small amount of by-product-water, then open the reaction kettle, and treat the product in a vacuum oven at 300°C for 3 hours to obtain an orange-yellow product. The rate is 94%.
Embodiment 2
[0020] Add 210g 4,4'-bis(3-aminophenoxybenzene) propane, 105g pyromellitic dianhydride, 2.32g phthalic anhydride and 12g triethylamine in autoclave under nitrogen protection, and then Close the reaction vessel, evacuate, inject carbon dioxide, heat the temperature to 50°C, and supplement the pressure of the reactor. When the temperature reaches 50°C, control the pressure of the reactor to 20MPa, turn on the electromagnetic stirring, and after 1 hour of reaction, raise the temperature to 180°C. Control the pressure of the reactor to 50MPa, continue the reaction for 8 hours, end the reaction, slowly open the vent valve, and control the venting time for 2 hours to remove a small amount of by-product-water, then open the reactor, and treat the product in a vacuum oven at 260°C After 3h, a light yellow product was obtained with a yield of 92%.
Embodiment 3
[0022]Add 98g 4,4'-diaminodiphenyl ether, 165g 4,4'-oxydiphthalic anhydride, 1.92g aniline and 12g triethylamine to the autoclave under nitrogen protection, then seal the reaction vessel, Vacuumize, feed carbon dioxide, heat the temperature to 50°C, supplement the pressure of the reactor, when the temperature reaches 60°C, control the pressure of the reactor to 20MPa, turn on the electromagnetic stirring, after 2 hours of reaction, raise the temperature to 200°C, control the pressure of the reactor to 50MPa, continue to react for 6h, end the reaction, slowly open the vent valve, control the vent time to 2 hours to remove a small amount of by-product-water, then open the reaction kettle, and treat the product in a vacuum oven at 280°C for 3h to obtain a yellow Product, the yield is 91%.
PUM
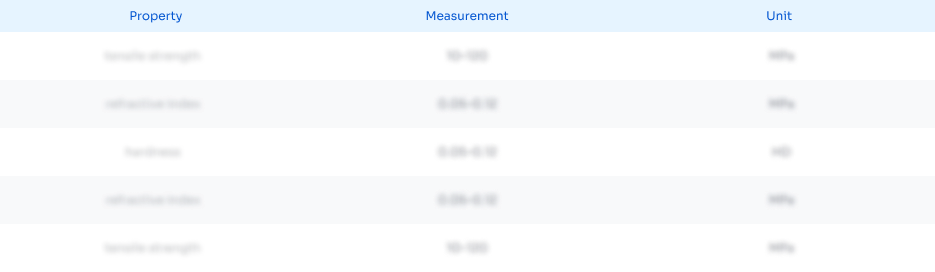
Abstract
Description
Claims
Application Information

- Generate Ideas
- Intellectual Property
- Life Sciences
- Materials
- Tech Scout
- Unparalleled Data Quality
- Higher Quality Content
- 60% Fewer Hallucinations
Browse by: Latest US Patents, China's latest patents, Technical Efficacy Thesaurus, Application Domain, Technology Topic, Popular Technical Reports.
© 2025 PatSnap. All rights reserved.Legal|Privacy policy|Modern Slavery Act Transparency Statement|Sitemap|About US| Contact US: help@patsnap.com