Core-shell structured nano-silica/polyacrylate emulsion and its preparation method
A technology of nano-silica and polyacrylate emulsion, which is applied in the preparation field of water-based core-shell structure nano-silica/polyacrylate composite emulsion, can solve the problem of high cost of reactive emulsifier, limitation of wide application, and inability to explain The relationship between the inorganic phase and the organic phase, etc., to achieve the effects of low equipment cost, obvious core-shell structure, and stable properties
- Summary
- Abstract
- Description
- Claims
- Application Information
AI Technical Summary
Problems solved by technology
Method used
Image
Examples
Embodiment 1
[0027] A. Add 820ml of ethanol, 30ml of deionized water, and 70ml of ammonia water into a reactor equipped with a condensing device and heat it to 50°C. After stirring evenly, add 40ml of tetraethyl orthosilicate, let it react for 24 hours, continue stirring and adjust the temperature to 35°C, then add 32ml of vinyltrimethoxysilane to the system, keep stirring at the temperature for 12 hours, after the reaction, separate the modified nano-silica particles, wash them with ethanol four times, and then disperse them in deionized water to obtain The mass concentration is 2.5% nano silicon dioxide dispersion liquid.
[0028] B. Add 10g of the silica dispersion in step A to the reactor equipped with a condensing device, then add 60g of deionized water, stir evenly, add 0.09g of sodium dodecylbenzenesulfonate and polyalkylphenol Composite emulsifier composed of oxyethylene ether and 0.3g acrylate monomer, heated to 78°C and stirred at a speed of 270rpm to disperse evenly, then slowly...
Embodiment 2
[0030] A. Add 850ml of ethanol, 30ml of deionized water, and 75ml of ammonia water into a reactor equipped with a condensing device and heat it to 50°C. After stirring evenly, add 45ml of tetraethyl orthosilicate, let it react for 22 hours, continue stirring and adjust the temperature to 30°C, then add 40ml of vinyltriethoxysilane to the system, keep stirring at the temperature for 13 hours, after the reaction, separate the modified nano-silica particles, wash them with ethanol four times, and then disperse them in deionized water. A nano-silica dispersion with a mass concentration of 2.3% was obtained.
[0031] B. Add 20g of the silica dispersion in step A to the reactor equipped with a condensing device, then add 55g of deionized water, stir evenly, add 0.09g of sodium dodecylsulfonate and octylphenyl poly Composite emulsifier composed of oxyethylene ether and 0.4g acrylate monomer, heated to 80°C and stirred at a speed of 300rpm to disperse evenly, then slowly add 9.6g acry...
Embodiment 3
[0033] A. Add 870ml of ethanol, 40ml of deionized water, and 77ml of ammonia water into a reactor equipped with a condensing device and heat it to 50°C. After stirring evenly, add 50ml of tetraethyl orthosilicate and allow it to react for 10 hours to obtain nano-silica Particles; when the preparation of monodisperse nano-silica particles is completed, continuously stir and adjust the temperature to 30°C, then add 20ml of vinyltrimethoxysilane to the system, keep stirring at the temperature for 13h, after the reaction, separate the modified The nano-silica particles were washed with ethanol four times and then dispersed in deionized water to obtain a nano-silica dispersion with a mass concentration of 2.9%.
[0034]B. Add 26g of the silica dispersion in step A to the reactor equipped with a condensing device, then add 54g of deionized water, and after stirring evenly, add 0.09g of sodium dodecylbenzenesulfonate and octylphenyl Composite emulsifier composed of polyoxyethylene et...
PUM
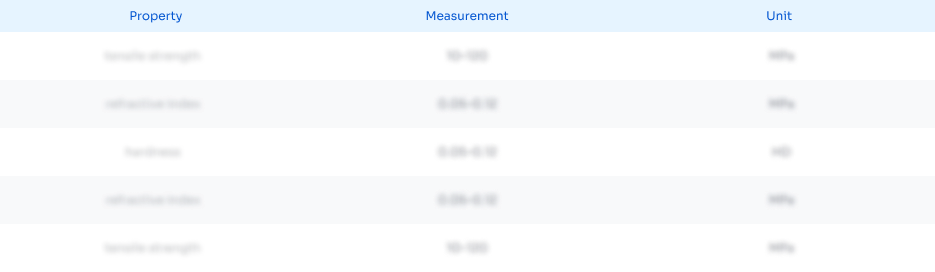
Abstract
Description
Claims
Application Information

- R&D
- Intellectual Property
- Life Sciences
- Materials
- Tech Scout
- Unparalleled Data Quality
- Higher Quality Content
- 60% Fewer Hallucinations
Browse by: Latest US Patents, China's latest patents, Technical Efficacy Thesaurus, Application Domain, Technology Topic, Popular Technical Reports.
© 2025 PatSnap. All rights reserved.Legal|Privacy policy|Modern Slavery Act Transparency Statement|Sitemap|About US| Contact US: help@patsnap.com