Through hole priority copper interconnection manufacturing method
A production method, through-hole priority technology, applied in semiconductor/solid-state device manufacturing, electrical components, circuits, etc., can solve problems such as high cost, achieve the effects of increasing production capacity, reducing etching steps, and reducing production costs
- Summary
- Abstract
- Description
- Claims
- Application Information
AI Technical Summary
Problems solved by technology
Method used
Image
Examples
Embodiment Construction
[0020] The method for manufacturing via-preferred copper interconnections of the present invention will be described in detail below in conjunction with specific embodiments and accompanying drawings.
[0021] refer to Figure 11 , the present invention provides a method for manufacturing through hole priority copper interconnection, comprising:
[0022] Step S1, depositing a dielectric layer on the substrate silicon wafer, coating a first photoresist on the dielectric layer, and forming a through-hole structure in the first photoresist, the first photoresist capable of forming a dura mater;
[0023] Step S2, in the same developing machine, coat the miniature cured material on the first photoresist pattern to cure the through-hole structure in the first photoresist, and heat the miniature cured material and reacting on the surface of the first photoresist, thereby forming an isolation film on the surface of the first photoresist;
[0024] Step S3, coating a second photoresi...
PUM
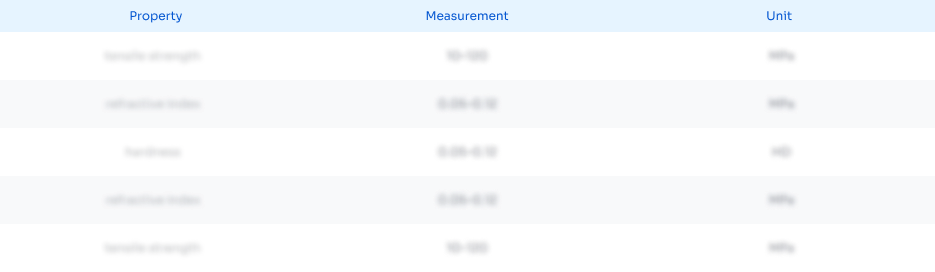
Abstract
Description
Claims
Application Information

- R&D Engineer
- R&D Manager
- IP Professional
- Industry Leading Data Capabilities
- Powerful AI technology
- Patent DNA Extraction
Browse by: Latest US Patents, China's latest patents, Technical Efficacy Thesaurus, Application Domain, Technology Topic, Popular Technical Reports.
© 2024 PatSnap. All rights reserved.Legal|Privacy policy|Modern Slavery Act Transparency Statement|Sitemap|About US| Contact US: help@patsnap.com