Method for making gas sensor based on natural color-sensitive material and porous TiO2 film
A technology of a gas sensor and a manufacturing method, which is applied in the direction of analyzing materials through chemical reactions and observing the influence of chemical indicators on materials, etc., which can solve the problems of narrow detection range, high cost, and unsuitability, and achieve The effect of wide detection range and high sensitivity
- Summary
- Abstract
- Description
- Claims
- Application Information
AI Technical Summary
Problems solved by technology
Method used
Image
Examples
Embodiment 1
[0023] Follow the steps below to implement:
[0024] 1. Choose one of silicon wafer, glass wafer, conductive glass wafer and polytetrafluoroethylene wafer as the substrate.
[0025] 2. Make gold or platinum electrodes on the substrate 1 by screen printing or plasma sputtering, such as figure 1 Substrate 1 and electrode 2 in.
[0026] 3. In this embodiment, TiO is prepared by sol-gel method 2 Porous membrane: weigh 1g TiO 2 Dissolve the powder in 2mL, 90%~100% acetic acid solution and 0.05mL, 90%~100% acetylacetone solution, grind in a mortar for 10min, then dissolve 0.5mL, 90%~100% OP emulsifier in 0.5 Add mL, 90%~100% alcohol slowly into the mortar, and continue grinding for 10min to make TiO 2 glue. Put the substrate 1 with the electrode 2 into 10% acetone solution, soak it for 12h, then dry it, and put the TiO 2 Apply the glue evenly on the substrate, dry it naturally for 10 minutes, put it in a muffle furnace at 300 °C for 1 hour, and make TiO after cooling. 2 Porou...
Embodiment 2
[0030] Follow the steps below to implement:
[0031] 1. Choose one of silicon wafer, glass wafer, conductive glass wafer and polytetrafluoroethylene wafer as the substrate.
[0032] 2. Make gold or platinum electrodes 2 on the substrate 1 by screen printing or plasma sputtering, such as figure 1 shown.
[0033] 3. In this embodiment, TiO is prepared by sol-gel method 2 For porous membrane, weigh 2.5g TiO 2 Dissolve the powder in 6mL, 90%~100% acetic acid solution and 0.3mL, 90%~100% acetylacetone solution, grind in a mortar for 20min, and then dissolve 0.3mL, 90%~100% OP emulsifier in 3mL, 90% Slowly add %~100% alcohol into the mortar and continue grinding for 20 minutes to make TiO 2 glue. Substrate 1 with electrode 2 is put into 20% acetone solution and dried after soaking for 24h, and TiO 2 Apply the glue evenly on the substrate, dry it naturally for 20 minutes, put it in a muffle furnace at 400 ° C for 2 hours, and make TiO after cooling. 2 Porous membrane3, such as...
Embodiment 3
[0037] Follow the steps below to implement:
[0038] 1、 One of silicon wafer, glass wafer, conductive glass wafer and polytetrafluoroethylene wafer is selected as the substrate.
[0039] 2. Make gold or platinum electrodes 2 on the substrate 1 by screen printing or plasma sputtering, such as figure 1 shown.
[0040] 3. Preparation of TiO by sol-gel method 2 Porous membrane: weigh 5g TiO 2 Dissolve the powder in 10mL, 90%~100% acetic acid solution and 0.5mL, 90%~100% acetylacetone solution and grind in a mortar for 40min, then dissolve 0.5mL, 90%~100% OP emulsifier in 5mL, 90 Slowly add %~100% alcohol into the mortar and continue grinding for 40 minutes to make TiO 2 glue. Soak the substrate with electrodes in 40% acetone solution for 48h and then dry it, and put the TiO 2 Apply the glue evenly on the substrate, let it dry naturally for 40 minutes, put it into a muffle furnace at 500°C for sintering for 3 hours, and make TiO after cooling. 2 Porous membrane3, such as ...
PUM
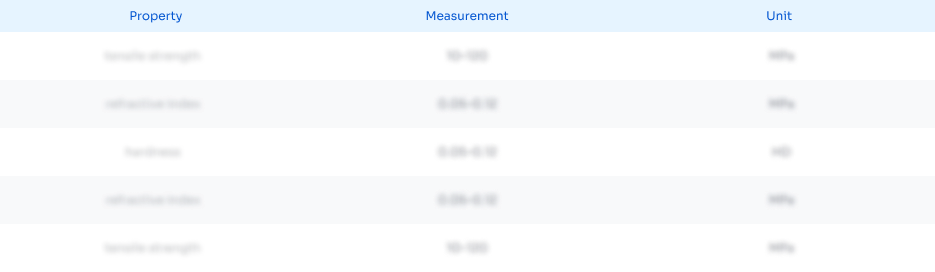
Abstract
Description
Claims
Application Information

- R&D Engineer
- R&D Manager
- IP Professional
- Industry Leading Data Capabilities
- Powerful AI technology
- Patent DNA Extraction
Browse by: Latest US Patents, China's latest patents, Technical Efficacy Thesaurus, Application Domain, Technology Topic, Popular Technical Reports.
© 2024 PatSnap. All rights reserved.Legal|Privacy policy|Modern Slavery Act Transparency Statement|Sitemap|About US| Contact US: help@patsnap.com