Thermal displacement correction method and thermal displacement correction device of machine tool
A thermal displacement, machine tool technology, applied in feeding devices, automatic control devices, computer control, etc., can solve problems such as thermal displacement errors
- Summary
- Abstract
- Description
- Claims
- Application Information
AI Technical Summary
Problems solved by technology
Method used
Image
Examples
no. 1 approach
[0072] refer to Figure 1~Figure 3 The thermal displacement correction device of the machine tool 1 according to the first embodiment will be described. figure 1 is an overall view of the machine tool 1 . figure 2 is a block diagram showing a thermal displacement correction device. image 3 It is a side view showing the deformed state of the column.
[0073] (Structure of machine tool 1)
[0074] Such as figure 1 As shown, the machine tool 1 has: a base 2, a column 10 (equivalent to the "support" of the present invention), a saddle 20 (equivalent to the "moving body" of the present invention), a spindle base 30, a table 40, and a numerical control Device 50 (equivalent to the "thermal displacement correction device" of the present invention). A guide rail in the Z-axis direction (a direction parallel to the ground) is formed on the upper surface of the base 2, and the base 2 is placed on the ground. The workpiece W is a machined component machined by the machine tool 1 ...
no. 2 approach
[0122] refer to Figure 6~Figure 8 The thermal displacement correction device of the machine tool 1 according to the second embodiment will be described. Image 6 is a block diagram showing the thermal displacement correction device 150 . Figure 7 It is an explanatory diagram of the calculation of the correction value. Figure 8 yes Figure 7 A partial enlargement of the . Here, the calculation method of the thermal displacement position of each inspection point in the thermal displacement correction inspection point position information acquisition process of the second embodiment is different from that of the first embodiment. The rest of the structure is substantially the same as that of the first embodiment, so detailed description is omitted.
[0123] Such as Image 6 As shown, the inspection point position information acquisition unit 160 of the thermal displacement correction device 150 of this embodiment includes a thermal displacement post-slope acquisition unit 1...
PUM
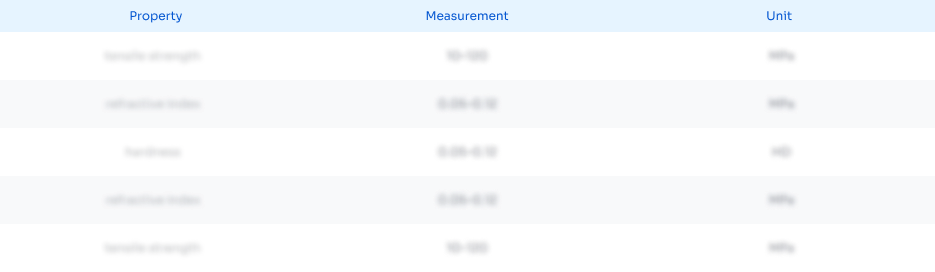
Abstract
Description
Claims
Application Information

- R&D Engineer
- R&D Manager
- IP Professional
- Industry Leading Data Capabilities
- Powerful AI technology
- Patent DNA Extraction
Browse by: Latest US Patents, China's latest patents, Technical Efficacy Thesaurus, Application Domain, Technology Topic, Popular Technical Reports.
© 2024 PatSnap. All rights reserved.Legal|Privacy policy|Modern Slavery Act Transparency Statement|Sitemap|About US| Contact US: help@patsnap.com