Production method of microalloyed tin bronze alloy
A micro-alloying and tin-bronze technology, which is applied in the field of preparation of micro-alloying tin-bronze alloys, can solve problems such as inapplicability, and achieve the effects of saving energy, reducing the degree of segregation, and small size
- Summary
- Abstract
- Description
- Claims
- Application Information
AI Technical Summary
Problems solved by technology
Method used
Image
Examples
Embodiment 1
[0031] Micro-alloyed tin-bronze alloy preparation method of the present invention, concrete steps are:
[0032] 1. Alloy melting: non-vacuum induction furnace is used for melting. Put the electrolytic copper into the smelting furnace, heat until the melt is completely melted, add a covering agent to keep it warm, after degassing and impurity removal, cover with burning charcoal, add the dried Cu-P master alloy and Sn, and stir well After standing;
[0033] 2. Microalloying treatment: add 0.2% cobalt refiner to the refined melt, and perform microalloying treatment at a high temperature of 1240-1300 ° C; The smelting temperature is consistent, and the microalloying treatment temperature refers to the temperature used in the existing alloy smelting;
[0034] 3. Alloy casting: Ingot casting of microalloying melt, the casting temperature is 1150-1250°C slightly lower than the temperature used in the above microalloying treatment, under the action of cooling conditions and refiner...
Embodiment 2
[0038] Micro-alloyed tin-bronze alloy preparation method of the present invention, concrete steps are:
[0039] 1. Alloy melting: non-vacuum induction furnace is used for melting. Put the electrolytic copper into the smelting furnace, heat until the melt is completely melted, add a covering agent to keep it warm, after degassing and impurity removal, cover with burning charcoal, add the dried Cu-P master alloy and Sn, and stir well After standing;
[0040] 2. Microalloying treatment: add 0.6% cobalt refiner to the refined melt, and perform microalloying treatment at a high temperature of 1240-1300 ° C; The temperature is consistent, and the microalloying treatment temperature refers to the temperature used in the existing alloy melting;
[0041] 3. Alloy casting: Ingot casting of microalloying melt, the casting temperature is 1150-1250°C slightly lower than the temperature used in the above microalloying treatment, under the action of cooling conditions and refiner cobalt, f...
Embodiment 3
[0045] Micro-alloyed tin-bronze alloy preparation method of the present invention, concrete steps are:
[0046] 1. Alloy melting: non-vacuum induction furnace is used for melting. Put the electrolytic copper into the smelting furnace, heat until the melt is completely melted, add a covering agent to keep it warm, after degassing and impurity removal, cover with burning charcoal, add the dried Cu-P master alloy and Sn, and stir well After standing;
[0047] 2. Microalloying treatment: add 1.0% cobalt refiner to the refined melt, and perform microalloying treatment at a high temperature of 1240-1300 ° C; The temperature is consistent, and the microalloying treatment temperature refers to the temperature used in the existing alloy melting;
[0048] 3. Alloy casting: Ingot casting of microalloying melt, the casting temperature is 1150-1250°C slightly lower than the temperature used in the above microalloying treatment, under the action of cooling conditions and refiner cobalt, f...
PUM
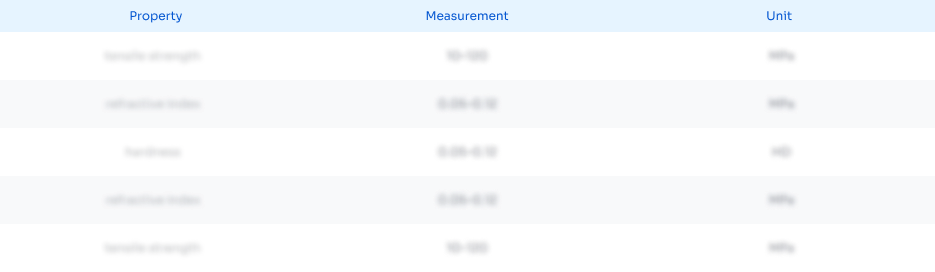
Abstract
Description
Claims
Application Information

- Generate Ideas
- Intellectual Property
- Life Sciences
- Materials
- Tech Scout
- Unparalleled Data Quality
- Higher Quality Content
- 60% Fewer Hallucinations
Browse by: Latest US Patents, China's latest patents, Technical Efficacy Thesaurus, Application Domain, Technology Topic, Popular Technical Reports.
© 2025 PatSnap. All rights reserved.Legal|Privacy policy|Modern Slavery Act Transparency Statement|Sitemap|About US| Contact US: help@patsnap.com