Method for functionalizing porous metal-organic framework materials, solid acid catalyst using same, and method for evaporating alcohol using the solid acid catalyst
A porous metal and organic framework technology, applied in organic chemistry, chemical instruments and methods, organic compound/hydride/coordination complex catalysts, etc., can solve problems such as high operating costs and uneconomical
- Summary
- Abstract
- Description
- Claims
- Application Information
AI Technical Summary
Problems solved by technology
Method used
Image
Examples
Embodiment 1
[0091] Embodiment 1 (functionalization of MIL-101 (Cr))
[0092] MIL-101(Cr)-AS was synthesized (Crystal Growth Design, 10, 1860, 2010 (Crystal Growth Design, 10, 1860, 2010)), and then 0.3 g of MIL-101(Cr) was added to a glass test tube using the material -AS, then add 20ml of DMF to make a suspension. After heating to 70° C., the suspension in the test tube was irradiated with ultrasonic waves for 60 minutes by using an ultrasonic generator (VC ×750, Sonic & materials). After cooling, the solid was collected by filtration and dried at 100° C. for 5 hours to obtain 0.25 g of refined MIL-101(Cr). 0.3g of MIL-101 (Cr) collected through 2 refinements was dried and cooled at 150°C under a vacuum condition of 0.8 pressure, and then 0.096g (1.25mmol) of cysteamine was added to 30ml of In ethanol, it was heated to reflux at 80°C for 8 hours. It was then filtered and dried to obtain 0.3 g of MIL-101(Cr) (referred to as MIL-101(Cr)-SH). Use 0.4g of MIL-101(Cr)-SH synthesized by th...
Embodiment 2
[0094] Embodiment 2 (using MIL-101 (Cr)-SO 3 Dehydration reaction of sorbitol in H)
[0095] Using the MIL-101(Cr)-SO obtained in Example 1 3 The H catalyst carried out the dehydration reaction of sorbitol. 10g of sorbitol and 0.2g of MIL-101(Cr)-SO 3 The H catalyst was added into a microwave reactor, and then reacted at 180° C. for 3 hours in a microwave oven (MARS-5, CEM Company). After the reaction, cooling was performed, the reactor was opened, and the solid catalyst was separated by filtration at high temperature. The obtained product was then dried at 110° C. to remove water. The composition of the product was analyzed using Acme 9000HPLC of Younglin Company equipped with RI detector and Asahipak NH2P-504E (No. N712004) column. The reaction conditions and results are briefly recorded in Table 1.
[0096] The dehydration conversion rate was 100%, and the yield of obtained isosorbide was 49.6%.
Embodiment 3
[0097] Embodiment 3 (using MIL-101 (Cr)-SO 3 H dehydration reaction of 2-butanol)
[0098] Using the MIL-101(Cr)-SO of 0.1g obtained in Example 1 3 H catalyst, carried out the dehydration reaction of 2-butanol with gas phase. The space velocity of the reactants is 1h -1 , the catalyst is dehydrated at 300°C, and the reaction temperature is 275°C. Such as image 3 As shown, it was confirmed by GC that butenes can be easily obtained by the dehydration reaction, and the catalyst performance can be stably maintained for more than 4 hours.
PUM
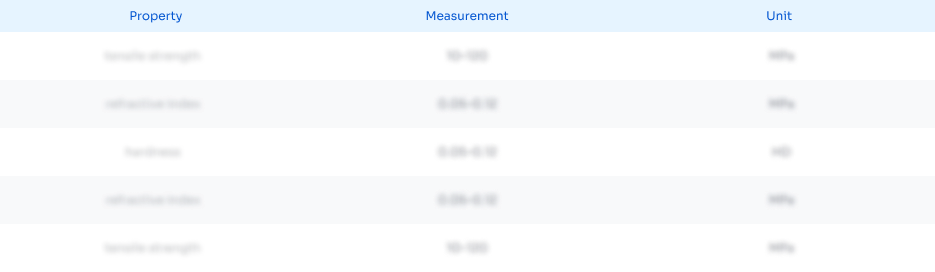
Abstract
Description
Claims
Application Information

- R&D
- Intellectual Property
- Life Sciences
- Materials
- Tech Scout
- Unparalleled Data Quality
- Higher Quality Content
- 60% Fewer Hallucinations
Browse by: Latest US Patents, China's latest patents, Technical Efficacy Thesaurus, Application Domain, Technology Topic, Popular Technical Reports.
© 2025 PatSnap. All rights reserved.Legal|Privacy policy|Modern Slavery Act Transparency Statement|Sitemap|About US| Contact US: help@patsnap.com