Lithium ion battery slurry, preparation method of the lithium ion battery slurry, and lithium ion battery
A lithium-ion battery and slurry technology, applied in battery electrodes, non-aqueous electrolyte battery electrodes, mixing methods, etc., can solve problems such as affecting battery capacity, existing preferential reaction points, and uneven electrode sheet dressings.
- Summary
- Abstract
- Description
- Claims
- Application Information
AI Technical Summary
Problems solved by technology
Method used
Image
Examples
preparation example Construction
[0024] A method for preparing lithium-ion battery slurry in an embodiment includes the following steps.
[0025] Step S101 , using an adhesive to prepare a glue solution with a concentration of 3%-7%.
[0026] The adhesive can be dissolved in a solvent to form a glue solution with a mass concentration of 3% to 7%. Among them, the binder is preferably one of styrene-butadiene rubber (SBR), sodium carboxymethyl cellulose (CMC), polyvinylidene fluoride (PVDF), polyacrylate, polyurethane or a mixture thereof. The solvent can be a common solvent, preferably water or N-methylpyrrolidone (NMP). The concentration of the above-mentioned glue solution cannot be made too high, preferably in the range of 3% to 7%. The glue solution of this concentration is easy to prepare, and can reduce the formation of micelles when added to the powder later.
[0027] Step S102, uniformly mixing the active material and the conductive agent in a three-arm planetary mixer at a low speed to form a powder...
Embodiment 1
[0050] Put a certain proportion of graphite and carbon black into a three-arm planetary mixer, and mix uniformly for 10 minutes at a speed of 5 rpm to form a powder. Weigh NMP with a mass ratio of 50:50 to the powder. After mixing the mixed powder with 8% of the total NMP for one hour, add the remaining 92% of NMP and 35% of the total glue solution for the first dilution, and pass hot water of 50 degrees into the jacket Heat was applied with stirring at top speed for 1.5 hours. Then add the remaining 65% of the glue for the second dilution, first stir at low speed for 10 minutes, and then stir at the highest speed for 2 hours to form a slurry.
Embodiment 2
[0052] A certain proportion of LiFePO 4 and carbon nanotubes were put into a three-arm planetary mixer, and mixed uniformly for 30 minutes at a speed of 8 rpm to form a powder. Weigh NMP with a powder mass ratio of 55:4. After mixing the mixed powder with 1% of the total NMP for one hour, add the remaining 99% of NMP and 20% of the total glue for the first dilution, and pass hot water at 40 degrees into the jacket Heat was applied with stirring at top speed for 1.5 hours. Then add the remaining 80% glue solution for the second dilution, first stir at low speed for 5 minutes, and then stir at the highest speed for 5 hours to form a slurry.
PUM
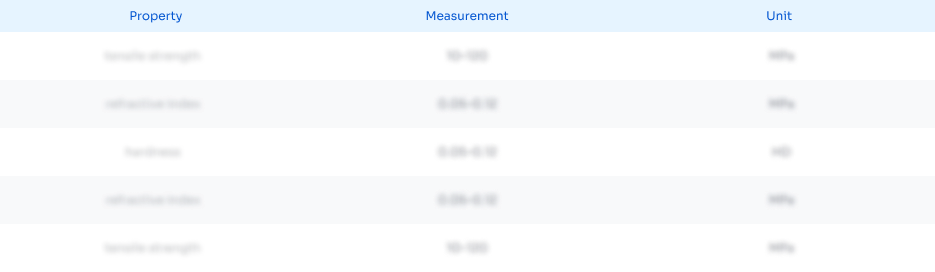
Abstract
Description
Claims
Application Information

- R&D
- Intellectual Property
- Life Sciences
- Materials
- Tech Scout
- Unparalleled Data Quality
- Higher Quality Content
- 60% Fewer Hallucinations
Browse by: Latest US Patents, China's latest patents, Technical Efficacy Thesaurus, Application Domain, Technology Topic, Popular Technical Reports.
© 2025 PatSnap. All rights reserved.Legal|Privacy policy|Modern Slavery Act Transparency Statement|Sitemap|About US| Contact US: help@patsnap.com