Process for preparing tetramethyldivinyldisilazane by conversion of divinyl tetramethyl disiloxane
A technology of tetramethyldivinyldisilazane and tetramethyldivinyldisilazane is applied in the field of preparation of tetramethyldivinyldisilazane and can solve the problem of tetramethyldivinyldisilazane. The problems of small disilazane output and high production cost can achieve the effect of avoiding ammonia waste, thorough reaction and solving pollution
- Summary
- Abstract
- Description
- Claims
- Application Information
AI Technical Summary
Problems solved by technology
Method used
Image
Examples
Embodiment 1
[0021] As shown in the figure, the preparation process steps of converting tetramethyldivinyldisiloxane into tetramethyldivinyldisilazane are:
[0022] 1. Esterification reaction: first put 1200 kg of concentrated sulfuric acid into the dripping tank, then put 800 kg of tetramethyldivinyldisiloxane and 2000 kg of petroleum benzene into the stirring tank, mix and stir for one hour; then pour into the stirring tank Concentrated sulfuric acid was added dropwise, and the dropwise addition was completed within two hours. During the reaction, a gas phase balance device was used to prevent volatilization of benzene and tetramethyldivinyldisiloxane, which not only reduced material loss, but also prevented environmental pollution. The temperature was controlled at 60 Below ℃; stop stirring after the reaction is over, keep the layers static for 60 minutes, release the dilute sulfuric acid at the bottom, and import the crude product of the upper layer into the ammoniation kettle;
[0023...
Embodiment 2
[0027] As shown in the figure, the preparation process steps of converting tetramethyldivinyldisiloxane into tetramethyldivinyldisilazane are:
[0028] 1. Esterification reaction: first put 1000 kg of concentrated sulfuric acid into the dripping tank, then put 600 kg of tetramethyldivinyldisiloxane and 1800 kg of petroleum benzene into the stirring tank, mix and stir for one hour; then pour into the stirring tank Concentrated sulfuric acid was added dropwise, and the dropwise addition was completed within two hours. During the reaction, a gas phase balance device was used to prevent volatilization of benzene and tetramethyldivinyldisiloxane, which not only reduced material loss, but also prevented environmental pollution. The temperature was controlled at 60 Below ℃; stop stirring after the reaction is over, keep the layers static for 60 minutes, release the dilute sulfuric acid at the bottom, and import the crude product of the upper layer into the ammoniation kettle;
[0029...
Embodiment 3
[0033] As shown in the figure, the preparation process steps of converting tetramethyldivinyldisiloxane into tetramethyldivinyldisilazane are:
[0034] 1. Esterification reaction: first put 1400 kg of concentrated sulfuric acid into the dripping tank, then put 1000 kg of tetramethyldivinyldisiloxane and 2200 kg of petroleum benzene into the stirring tank, mix and stir for one hour; then pour into the stirring tank Concentrated sulfuric acid was added dropwise, and the dropwise addition was completed within two hours. During the reaction, a gas phase balance device was used to prevent volatilization of benzene and tetramethyldivinyldisiloxane, which not only reduced material loss, but also prevented environmental pollution. The temperature was controlled at 60 Below ℃; stop stirring after the reaction is over, keep the layers static for 60 minutes, release the dilute sulfuric acid at the bottom, and import the crude product of the upper layer into the ammoniation kettle;
[003...
PUM
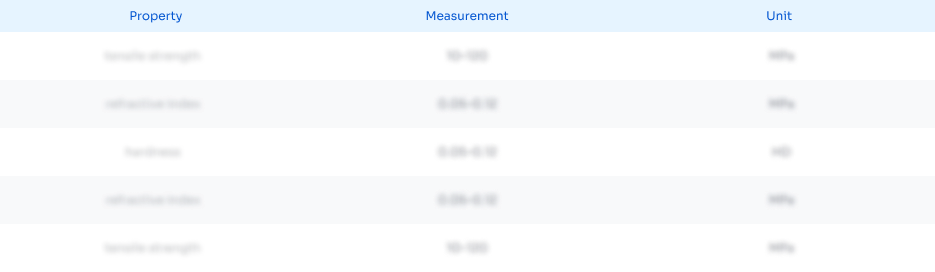
Abstract
Description
Claims
Application Information

- R&D
- Intellectual Property
- Life Sciences
- Materials
- Tech Scout
- Unparalleled Data Quality
- Higher Quality Content
- 60% Fewer Hallucinations
Browse by: Latest US Patents, China's latest patents, Technical Efficacy Thesaurus, Application Domain, Technology Topic, Popular Technical Reports.
© 2025 PatSnap. All rights reserved.Legal|Privacy policy|Modern Slavery Act Transparency Statement|Sitemap|About US| Contact US: help@patsnap.com