Method for computing ultrasonic guided-wave acoustic-elastic frequency dispersion of prestress waveguide structure
A technology of waveguide structure and ultrasonic guided wave, which is applied in computing, special data processing applications, instruments, etc., can solve problems such as lack of universality, large calculation errors, unscientific economy, etc., and achieve the effect of saving manpower and high precision
- Summary
- Abstract
- Description
- Claims
- Application Information
AI Technical Summary
Problems solved by technology
Method used
Image
Examples
Embodiment Construction
[0024] In conjunction with the content of the method of the present invention, the following example of the calculation method of the longitudinal mode acoustic elastic constant in the axisymmetric bar is provided, and the specific steps are as follows: figure 1 Shown:
[0025] 1) The material is No. 45 steel with a density of 7843kg / m 3 , using the third-order elastic constant test method of body wave, the measured second-order Lame constants are: λ=111.59GPa, μ=81.79GPa; the third-order Murnaghan constants are: l=-81.25GPa, m=-583.1GPa, n=-782.85GPa;
[0026] 2) Using the Murnaghan hyperelastic model to model the waveguide structure, the constitutive relation of this model is: In the formula, is the initial strain of prestress, e ζη is the acoustic small perturbation strain E γδ the linear part of . The diameter of the model is selected as 20mm, and the length of the model is selected as 1000mm;
[0027] in:
[0028] C αβγδ =C γδαβ , C αβγδζη =C αβζηγδ =C ζηαβ...
PUM
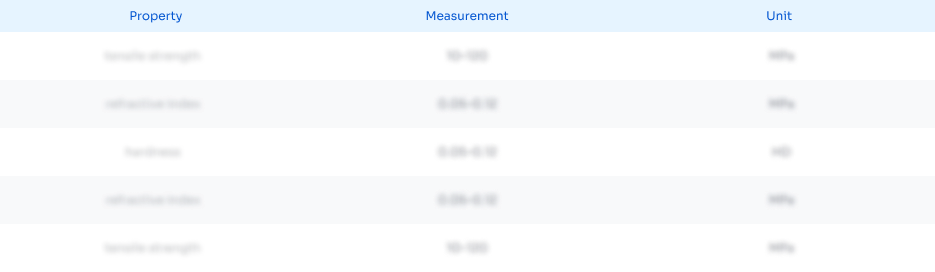
Abstract
Description
Claims
Application Information

- R&D
- Intellectual Property
- Life Sciences
- Materials
- Tech Scout
- Unparalleled Data Quality
- Higher Quality Content
- 60% Fewer Hallucinations
Browse by: Latest US Patents, China's latest patents, Technical Efficacy Thesaurus, Application Domain, Technology Topic, Popular Technical Reports.
© 2025 PatSnap. All rights reserved.Legal|Privacy policy|Modern Slavery Act Transparency Statement|Sitemap|About US| Contact US: help@patsnap.com