Machine printing binder for printing textiles and preparation method thereof
A textile and printing technology, which is applied in the field of machine printing glue for textile printing, can solve the problems of poor elasticity, sticky printing glue, loss of small dots, etc., achieve good elasticity, no cracking when stretched, and solve the problem of antifreeze Effect
- Summary
- Abstract
- Description
- Claims
- Application Information
AI Technical Summary
Problems solved by technology
Method used
Image
Examples
Embodiment
[0038] Machine printing antifreeze transparent paste:
[0039]The first step is to add 100g of H-260 acrylic emulsion into the experimental kettle, and then add 40g of 1380 water polyurethane resin. After mixing, put the material on the stirring disperser for medium and low speed stirring, and the rotation speed is preferably 500r / min. Keep this speed to disperse and stir for about 10 minutes;
[0040] The second step is to keep stirring and dispersing machine at 500r / min to continue stirring, and then add 20g of glycerol, 20g of deionized water, 1g of 502C defoamer, 4g of 46 high-performance anti-adhesive agent, 2g of S-15 anti-adhesive hand feeling additive, S-21 water-based wax emulsion 6g. After adding all of it, increase the speed of the stirring and dispersing machine to 1000-1200r / min, and disperse and stir for 5 minutes;
[0041] Step 3: After the above materials are uniformly dispersed, add 0.6g of AMP-95 multifunctional regulator, and disperse for 3min at the speed ...
PUM
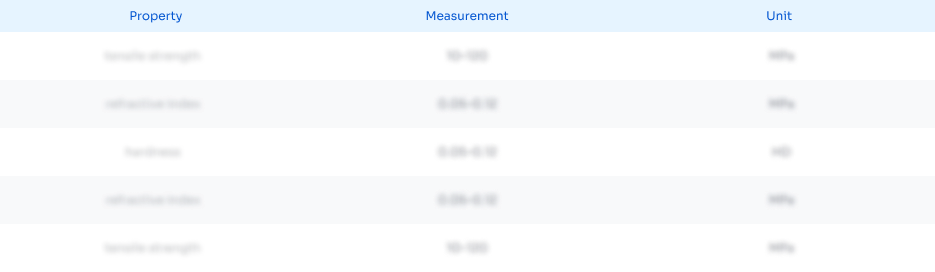
Abstract
Description
Claims
Application Information

- Generate Ideas
- Intellectual Property
- Life Sciences
- Materials
- Tech Scout
- Unparalleled Data Quality
- Higher Quality Content
- 60% Fewer Hallucinations
Browse by: Latest US Patents, China's latest patents, Technical Efficacy Thesaurus, Application Domain, Technology Topic, Popular Technical Reports.
© 2025 PatSnap. All rights reserved.Legal|Privacy policy|Modern Slavery Act Transparency Statement|Sitemap|About US| Contact US: help@patsnap.com