Dressing method for high-phosphor-content oolitic hematite
A technology of oolitic hematite and ore beneficiation method, which is applied in the direction of chemical instruments and methods, flotation, wet separation, etc., can solve the problems of low grade, insignificant effect, difficulty in obtaining satisfactory separation indicators, etc., and achieve reduction in operation load, low price, and easy on-site operation
- Summary
- Abstract
- Description
- Claims
- Application Information
AI Technical Summary
Problems solved by technology
Method used
Examples
Embodiment 1
[0021] A beneficiation method for high-phosphorus oolitic hematite. It is characterized in that the main chemical composition of the high-phosphorus oolitic hematite entering the beneficiation operation is: Fe 2 o 3 30~37wt%, SiO 2 12~18wt%, Al 2 o 3 5~9wt%, Na 2 O is 0.08~0.15wt%, K 2 O is 0.6-1 wt%, CaO is 2-3 wt%, MgO is 0.6-1 wt%, and P is 1-2 wt%.
[0022] The beneficiation method of the present embodiment comprises the following steps:
[0023] The first step of grinding: the oolitic hematite is crushed to a particle size of -20mm~-30mm, and then the ore is sent to the grinding machine, and the high-phosphorus oolitic hematite is continuously ground in two stages until the ore fineness is less than 0.074mm About 80wt% or more;
[0024] The second step of desliming: the ore pulp after grinding is removed through the desliming bucket to remove the slime less than 0.020mm;
[0025] The third step of magnetic separation: the deslimed pulp goes through two strong mag...
Embodiment 2
[0033] A beneficiation method for high-phosphorus oolitic hematite. It is characterized in that the main chemical composition of the high-phosphorus oolitic hematite entering the beneficiation operation is: Fe 2 o 3 38~45wt%, SiO 2 16~21wt%, Al 2 o 3 4~7wt%, Na 2 O is 0.06~0.15wt%, K 2 O is 0.4-1.2 wt%, CaO is 1-3 wt%, MgO is 0.5-1.5 wt%, and P is 1.5-2.5 wt%.
[0034] The beneficiation method of the present embodiment comprises the following steps:
[0035] The first step of grinding: the oolitic hematite is crushed to a particle size of -20mm~-30mm, and then the ore is sent to the grinding machine, and the high-phosphorus oolitic hematite is continuously ground in two stages until the ore fineness is less than 0.074mm About 95wt% or more;
[0036] The second step of desliming: the ore pulp after grinding is removed through the desliming bucket to remove the slime less than 0.025mm;
[0037] The third step of magnetic separation: the deslimed pulp goes through two st...
PUM
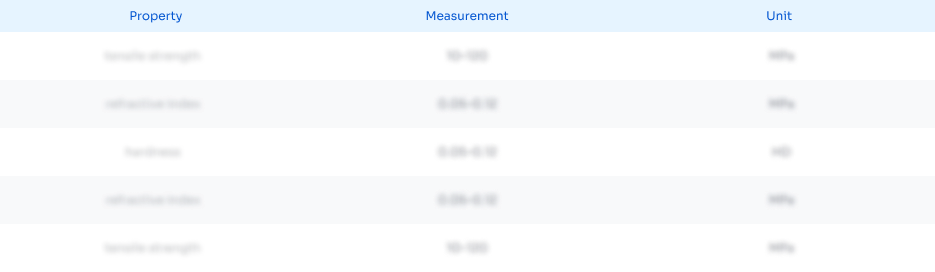
Abstract
Description
Claims
Application Information

- Generate Ideas
- Intellectual Property
- Life Sciences
- Materials
- Tech Scout
- Unparalleled Data Quality
- Higher Quality Content
- 60% Fewer Hallucinations
Browse by: Latest US Patents, China's latest patents, Technical Efficacy Thesaurus, Application Domain, Technology Topic, Popular Technical Reports.
© 2025 PatSnap. All rights reserved.Legal|Privacy policy|Modern Slavery Act Transparency Statement|Sitemap|About US| Contact US: help@patsnap.com